2. User Interface¶
2.1. Overview of WANDA 4 features¶
2.1.1. MSOffice look and feel¶
Multiple documents support.
Full drag and drop support.
Full clipboard support.
MS office like tool bars.
MS office like menus.
2.1.2. Diagrams¶
Wanda 4 uses iGrafx FlowCharter 2017 as diagram engine.
Full drag and drop support.
Copy and move objects and their data between one or multiple documents.
Clipboard support to Word/Excel.
Export a diagram to HTML.
Export a diagram to AutoCAD.
Export a diagram to Visio.
Enhance a diagram with your own text and drawings.
Multiple layer support (you can hide and protect layers easily).
Use your own pictures/maps as background (bmp, gif, autocad, coreldraw, wmf).
Different line styles / weights / colours supported.
Zoom support.
Quick zoom to selection.
Auto fit your printed diagram to m-by-n pages.
Direct feedback to the user. The diagram is real-time validated.
Components with empty/incorrect properties can be easily selected. The diagram window scrolls automatically to the invalid component if the component is out of side.
Vector based and object based schematisation.
Components including connection lines are automatically rotated when you add them in vector based mode.
Hydraulic nodes are automatically recognised. Multiple lines that are connected to each other are recognised as one single calculation node.
Custom-made shape libraries. Deltares can design shape libraries with customer specific components. You can use different shape libraries simultaneously.
Protect your diagrams and properties by a password.
Optionally visible grid.
Optionally snap objects automatically to grid.
2.1.3. Routes in diagram¶
You can quickly select a route/path through your diagram by selecting the first and last component in the route.
You can quickly ‘align to line’/’rotate’/’reverse a route’.
Selections that contain an unambiguous sequence of pipes are automatically recognised as route.
Selections and routes can be stored using a keyword.
You can see simultaneously an unlimited number of (moving) chart series of different routes.
You can see the overall extremes and total length of a route.
You can build routes with different pipe orientations (results are automatically ‘flipped’)
2.1.4. Automatic name generation¶
Components and connections are automatically named.
If you assign a name that already exists or if you copy an existing component a new unique name based on the existing name is assigned to the new component. If the name ends with a number, this number is increased, otherwise a character is added to the name.
You can rename a selection of components / connections with a single mouse click.
2.1.5. Property text boxes¶
View properties (input and output) of hydraulic components directly in text boxes in the diagram.
You can visualise output directly in the diagram for the active time step (see How to use the Time Navigator).
You can visualise output extremes directly in the diagram.
You can specify the properties that you want to see in the diagram.
You can easily move property text boxes in the diagram.
Property text boxes are always attached to a component or connection. Text boxes are automatically moved/deleted/copied when the component or connections moved/deleted/copied.
Property text boxes are placed in a separate layer. This layer can be made hidden. When this text layer is active you can easily move and change the font attributes of those property text boxes.
Property text boxes are also visible when you print the diagram.
The properties ‘Comment’, ‘Model name’ and ‘Reference ID’ (for pipes only) have been included to support a traceable modelling in accordance with ISO 9001.
2.1.6. Property list windows¶
The main property window displays the properties of all components and connections in diagram selection.
You don’t have to open a separate dialog every time you want to inspect/edit an object. The main property window is instantly adjusted when the diagram selection changes.
You can simply select one or more objects and view/edit this objects at once.
You can open an unlimited number of extra property windows that show a single object.
Input and output together in one list.
You can choose to see the output for the active time step (see How to use the Time Navigator) or to see the extremes in the simulated time period.
Drag and drop support between two property lists.
Easily select properties in the same way you select files in a file manager/explorer. A property that you edit is automatically selected.
Quick synchronisation of selected properties between objects.
Easily compare properties (and tables) from two or more hydraulic components (different values are highlighted in red).
Direct access to all tables from the property list of a hydraulic component with one mouse click.
Write the selected properties to a template file.
Easily change properties by loading a template file (or dropping a template file in the property list window). The loaded properties are automatically selected/highlighted. If you have loaded the wrong template file you can simply press the undo button.
Easily connect you own programs/databases to the property list by using the clipboard or template files.
Opening a time or location chart of one property by pressing the chart button of a property.
Add a property to a chart by dragging a chart button to any chart you like.
Enter values with other units than the active unit group.
View the property value in every available unit for the property dimension at once.
Optionally hide the input or output data.
Overall view of all the selected components. In this view you see the (extreme) values of all the properties available in the selected components.
Change the component type without losing the property values and tables.
Rollback/Undo support.
User name property. The name of the user that made a change to a component is added to the user name property of the changed component.
Modified property. This property shows the last date/time the selected component was changed.
2.1.7. Table editor¶
The table data can be visualised in a chart next to the table. This chart is automatically updated while you are typing.
Easy adding or removing (multiple) rows.
Clipboard support within one table editor.
Clipboard support between two table editors.
Clipboard support between one table editor and Excel/Word.
Simple numerical operations (+, -, x, /) to a range of table values.
Auto fill missing values by linear interpolation.
Print management.
2.1.8. Spreadsheet¶
Spreadsheet can be used to edit or view properties of several components simultaneously.
Create a spreadsheet of the diagram selection and selected properties in the property window by one single mouse click.
Unlimited number of different spreadsheets from one or more documents.
Components are sorted by type and name.
Column width is automatically adjusted to fit all values.
You can transpose the spreadsheet. This way you can display components side by side as well as above each other.
You can display extreme values instead of the values of the active time step (see How to use the Time Navigator).
When you print a spreadsheet you can automatically fit to m-by-n pages (portrait and landscape).
Print headers and footers are automatically updated.
You can copy a selection to Excel using the clipboard.
Navigation coupling between spreadsheet and diagram.
2.1.9. Calculations¶
Fast calculations.
Change something and see the impact of that change in all open windows.
Stop and resume transient calculations.
You can stop a transient calculation before the simulation has ended. When the calculation is stopped you can see the results so far. You can change action tables to interact with the results before you continue the calculation.
Background calculations. While a calculation is in progress you can inspect the running document or continue with another document.
You can calculate multiple documents sequentially (like printer jobs).
Create child cases from parent case
Repeat calculations with varying some input parameters as defined in a simple parameter script; specified output summarised in compact table
You can disuse components temporarily instead of deleting them from the diagram. It is possible to hide parts of the diagram for the calculation kernel. Disused components are greyed out in the diagram. You need one look to see the differences between variants, if you disuse components instead of deleting them.
2.1.10. Chart engine¶
Drop multiple series (from different documents) into the chart.
Moving location series supported (picture for active time step, see How to use the Time Navigator).
Frozen location series supported. Frozen series show one fixed time step.
Chart time cursor. A vertical blue line gives the active time step in time charts (see How to use the Time Navigator).
View as many charts simultaneously as you want
All open charts support moving series and are automatically updated when input or output is changed.
Create your own custom dedicated chart templates.
Export the chart data to a spreadsheet using the clipboard.
Export the chart to a WMF/JPG/BMP/GIF picture.
Paste the chart in Word using the clipboard.
Series are automatically removed when the (belonging) hydraulic component is deleted or the document is closed.
The chart is automatically closed when it is empty.
Zoom and scroll supported by mouse.
Chart headers and chart footers are automatically updated.
2.1.12. Unit groups¶
Quickly switch between different unit groups.
All property lists, tables, tabular views and charts are immediately adjusted to the active unit group.
User customised unit group.
2.1.13. Selection builder¶
Quickly (de)select components/connections by a property, value and operator (<, <=, =, <>, >=, >, like).
Existing keywords, component types, model names and user names are listed by a drop down list.
Add/Remove keywords to/from a selection.
Smart zoom/scroll. If not every selected object is visible the view extend is adjusted to see every selected object.
2.1.14. ‘On demand’ data loading / Smart saving¶
Quick access to output data of existing documents.
Complicated documents with large output data (100Mb) are loaded within seconds.
Changes are only saved at the moment you save explicitly. If your computer goes down your last saved documents are unchanged/undamaged.
Only changes are saved. This makes it possible to save slightly changed large documents within a second.
2.1.15. Instant window/view refresh¶
Every (implicit) change is directly reflected in all open views (diagrams, property lists, tables, tabular views and charts).
Any recalculation is directly reflected in all open views. You do not have to reselect your output after recalculation.
2.2. Getting Started¶
2.2.1. Hydraulic analysis - Functional steps¶
Examining a hydraulic study of a pipeline system depends on the objectives of the study. A typical sequence is shown in the diagram beneath.
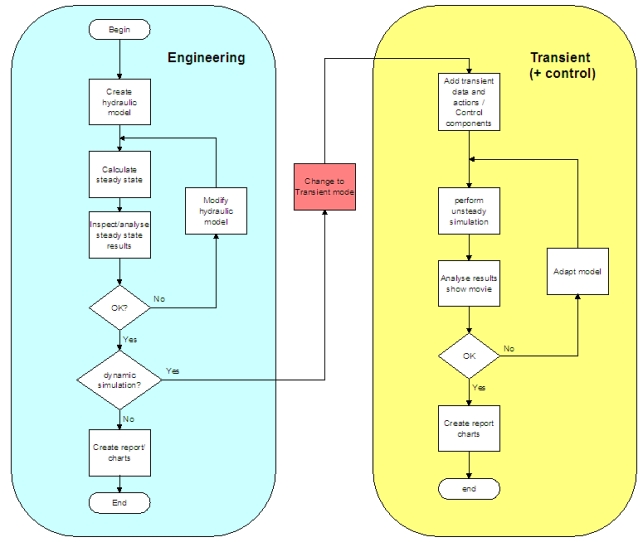
In Engineering mode only so-called steady state calculations can be performed. You have no access to the unsteady state simulation to carry out dynamic phenomena. Only input parameters necessary for the steady state (resistance) calculations must be entered. Changing to Transient mode (menu bar: model/change mode & options) all additional data for the unsteady state becomes accessible.
Opening a new document; it always start in Engineering mode
2.2.1.1. Create the hydraulic model¶
The first step is to create the schematic diagram of the pipe system and enter component specific hydraulic input data such as geometry, size and other characteristics. This is called “the hydraulic model”. It must be completed successfully before the user may proceed with the actual computation of steady and transient flow.
The most essential function of this part is the conception of the hydraulic model and input of the component specific hydraulic data.
The hydraulic model is in fact a schematic drawing of the actual pipe system, using lines and easy-to-read symbols that represent different elements in the system. It defines all the components in the pipe system with respect to their class and the way they are connected. The conception of the model is realised in the diagram user interface and is fully mouse-operated. WANDA has been designed in such a way that a model can be created with minimum efforts.
The numerical hydraulic data specific to each component are entered via the property windows.
2.2.1.2. Calculate steady state¶
WANDA computes the steady state. The results are used as the initial conditions for the computation of the unsteady state. steady has no dialogue with the user.
2.2.1.3. Specify hydraulic actions¶
(Applicable to WANDA Transient only; change to Transient mode using menu model/ mode & options)
In WANDA one can specify the total simulation time and hydraulic actions. Hydraulic actions, such as manipulation of a valve, pump trip or prescribed changes in pressure head or delivery rates, cause hydraulic transients.
Actions are specified in the property window of the particular H-component.
2.2.1.4. Calculate transient¶
(Applicable to WANDA Transient only; change to Transient mode using menu model/ mode & options)
WANDA also computes the transient flow. This is a separate task. If you unhide this task form the taskbar, the progress in computation including logging messages can be monitored. The estimated time for the simulation is displayed in the header (caption) of the diagram window. The user can interrupt the computation at any time. An interrupted computation can be resumed later on using the same simulation.
During the unsteady calculation the “real time” results can be followed. The user opens the selected graphic windows before starting a calculation. The graphics in these windows are regularly refreshed during the calculation (refresh time is set in model/time window). Looking to the progressing results, you can interrupt the simulation when you find them unsatisfactory. For example, when you evaluate a control system the behaviour of the control can be followed during the simulation. This way it is possible to reduce the simulation time.
Editing data after a calculation all old results remain visible, however coloured differently, and with a strike-through value.
2.2.1.5. Get results¶
WANDA has powerful utilities to show results. Selected data can be printed in standard report format. Location and/or time series can be put into charts and the dynamic flow process can be visualised using an internal movie feature. The data report and the charts can be displayed on screen, saved on disk or directly sent to the printer.
Printed data report
Printed data are useful for inspection of numerical values of calculated variables. The input and output report are adequately organised in a spreadsheet view, such that it can be included in any formal documentation of a waterhammer simulation.
Charts
These are useful for examining how the pressure or discharges vary as a function of time or along the pipes. Pressure waves travelling along the pipe system are easily recognised from a graph. Selection of the variable and settings of the chart are menu operated and require minimum effort.
The movie feature
The movie is used to visualise the dynamic behaviour of pressures and discharges along selected routes in the pipe system (see Time Navigator).
When the steady and transient state computations are completed, the user might sometimes not be interested in the absolute numbers of calculated variables. He may first want to get some insight into the physical flow process. Animated view of the flow variables using the movie feature will prove to be quite helpful for that purpose. Furthermore the extreme values are displayed in the movie chart. The movie can be recorded and save as AVI-file.
2.2.2. WANDA 4 - User Interface¶
In this section we will briefly explain how to use together the Component Gallery, the Property Window and the Diagram, in the construction of a hydraulic model.
See also:
Manual/Help iGrafx FlowCharter 2017
2.2.2.1. Introduction¶
When you start the application you see a screen that can be divided in three major parts.
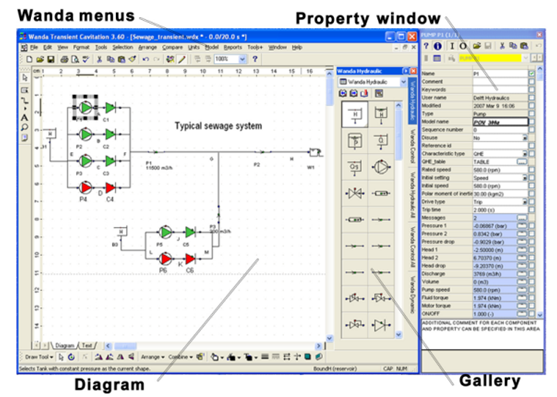
The Diagram in your first session will be empty of course.
The Diagram is the area where you will actually build the hydraulic model that you wish to calculate (see Building the diagram). You will build this model adding components from the Shape Library / Gallery.
The menu bar contains:
iGrafx Flowcharter menus (file/edit/view/insert/format/tools/arrange/window) and
WANDA menus (Selection/Compare/Units/Model/Report/Help).
The various WANDA Menus are used to:
quick selection of components to view or edit (see Selection Menu)
compare contents and show differences of two cases (see Compare menu)
choose the desired unit for view/edit (see Units Menu)
specify your other input data (see Model Menu)
view and report the results of your hydraulic model (see Reports Menu).
The diagram short cut menu (right mouse click) gives you fast access to the most important diagram features
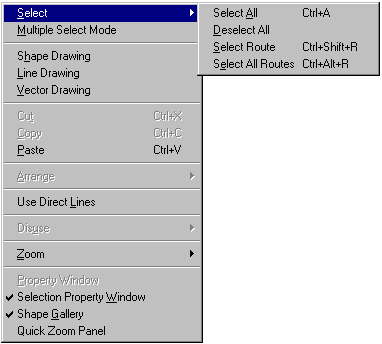
At the right side of your screen, the Property Window is displayed.
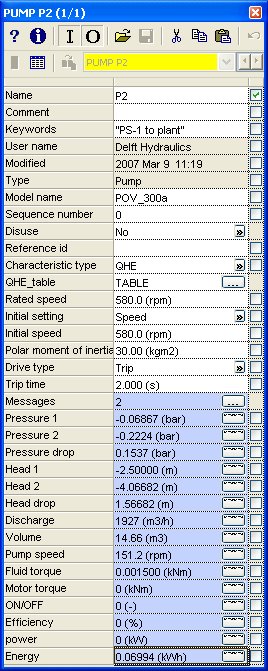
In this window you can see input and output of a (group of) selected component(s). The Property Window is one of the most important features. It helps you to navigate through your data. The short cut menu (right mouse click) gives you access to the most important property window features.
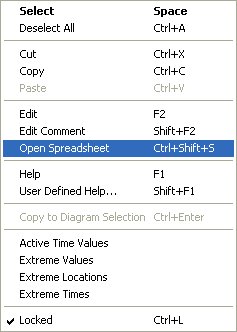
See for further detail: Property windows.
2.2.2.2. Dialog windows - General¶
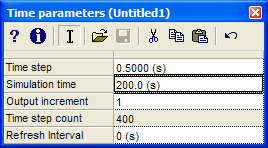
The appearance of all WANDA dialog windows the proceeding is the same, so that the user will get familiar with the program immediately.
All dialog windows contain:
a toolbar
a number of input boxes (white background)
a number of output boxes (blue background)
Toolbar

Most icons are self-explaining (copy, past, save, open, etc.). Read the tool tip to understand the feature.
Input, Output and Units
We would like to draw attention on the following three buttons in the toolbar:
Input boxes
For all characteristics, default values are supplied. If an input box is grey, no values can be entered. The values in the white boxes can be edited.
Output boxes
For all type of components calculated output values are displayed in boxes with a blue background. These values cannot be edited (read only).
2.2.2.3. Tooltips¶
ToolTips are short messages that appear in bubble text. These messages help to explain the name of the tool or button and, in some cases, what the tool or button does.
In WANDA all functions, buttons, icons, etc. have their own ToolTip. It is advisable to look at these tooltips first before selecting a WANDA 4 option.
2.2.3. WANDA 4 in 10 steps¶
2.2.3.1. Step 1. Add Components¶
2.2.3.2. Step 2. Connect Components¶
2.2.3.3. Step 3. Set Component properties¶
2.2.3.4. Step 4. Set other inputs¶
2.2.3.5. Step 5. Use advanced features¶
2.2.3.6. Step 6. Calculate steady state¶
2.2.3.7. Step 7. Specify hydraulic actions¶
2.2.3.8. Step 8. Calculate transient¶
2.2.3.9. Step 9. View output¶
2.2.3.10. Step 10. Report results¶
2.3. Building the diagram¶
For the diagram the incorporated program iGrafx Flowcharter is used. All features about diagram editing is explained in the separate Flowcharter Manual and Flowcharter Online Help.
In this chapter the WANDA related topics are explained.
2.3.1. Shape Library / Gallery¶
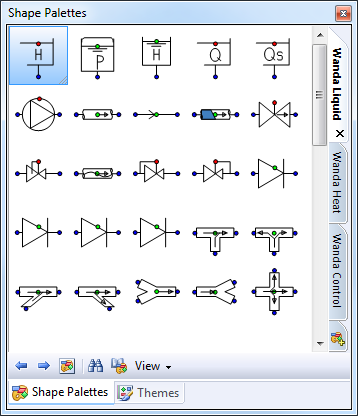
The default shape Libraries WANDA 4 shows are:
WANDA Liquid
WANDA Heat
WANDA Control
In the future new galleries will be introduced for other physical domains or hybrid components. Special made components for particular clients are stored in the “WANDA special” gallery.
To show the status of some active components, like PUMP and VALVE, WANDA uses a extra gallery “WANDA Dynamic” but this gallery will be hidden.
It is possible to assemble your own gallery which contains a subset of the standard galleries. This can be easy to use only one gallery with the frequent used components.
To create your own gallery, consult the iGrafx Help (Shape pallet, F9 – Media manager)
If the gallery is not visible, go to menu view /show gallery or click right in the diagram to activate short cut menu and check Gallery.
By dragging the components in the library you can change their order, or edit the size of the icons.
Default only the shape is visible in the gallery. The tooltip informs you about the particular type. To display this type in the gallery, use the right mouse menu
2.3.2. Adding components¶
You can add components in the diagram by selecting them in the gallery and dragging them into the Drawing Area.
For details on this subject we also refer to the iGrafx Flowcharter Help.
Each component gets automatically a name starting with the first character of the component type followed by a sequence number. This name can be changed in the property window. The combination “Component type + local Name” must be unique.
2.3.3. Looking closer at components in the diagram¶
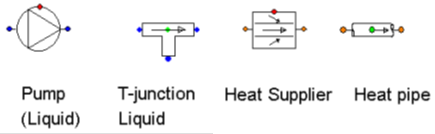
When we take a closer look at the components we see that they have several connect points in different colours. We distinguish physical connect points and control connect points. The physical connect points are used to connect other components which belong to the same physical domain. Therefore each domain has his own connect point colour: blue the Liquid domain, and orange for the heat domain.
It is not possible to connect different coloured connect points to each other
The red and green connect points are reserved for the control module
Note that the shape of a component indicates the positive flow direction if applicable (e.g. P1 and V1 in the picture above). You can change the flow direction by flipping or rotating the component in the Arrange Menu.
For details on this subject we also refer to the iGrafx Flowcharter Help.
2.3.4. Connecting components¶
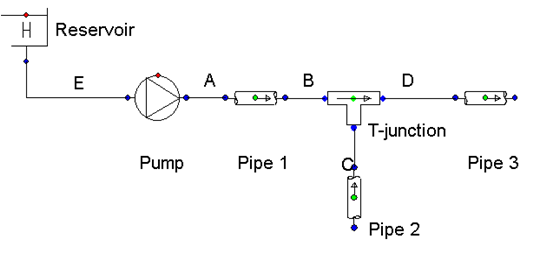
Connecting components is as simple as adding them. All you’ve got to do is select a component and drag the mouse pointer to another component.
To switch to line mode, activate the right mouse click menu and choose “Line drawing mode”
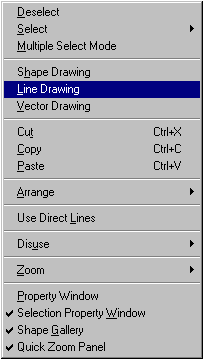
You can also use the Connector Line Tool from the Toolbox, left of the Diagram.
For WANDA 4 diagrams, it is recommended to use only the first three types from the menu below.
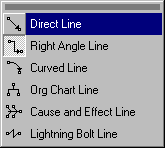
See also iGrafx Flowcharter Help for details on drawing and manipulating connections.
2.3.4.1. Master and Slave connections¶
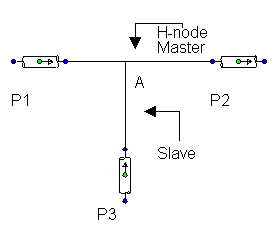
The H-node is represented by at least one single (master) connection line that can connect none, one or two H-components. With extra slave lines it’s possible to connect more than two H-components to one H-node
A connection line that is NOT connected to any other line is called a master line. The first connection line you draw is always a master line. Slave lines are connected by ONE end to another master or other slave line. It is not allowed to draw a line between two other lines.
If you select a connection line both ends are marked with a square. The colour of this square is very important. When the square is red it tells you that the line is connected to another line or component. If the square is black the line end is connected to nothing. It’s possible that a line is visually connected but is not connected for Wanda. In this case you see a black square at the fake connected end of the line. When you press the pause button while the property window is active you can see the connectivity of h-components and h-nodes used by Wanda.
The easiest way to fully understand connections is to draw some arbitrary connection lines. If you draw something that is not allowed (schematically) Wanda popup a message and deletes the illegal lines”.
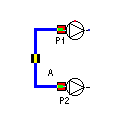
Step 1. Adding connection A (master) between P1 and P2
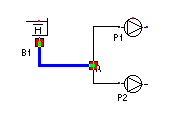
Step 2. Adding connection (slave) from B1 on to connection A
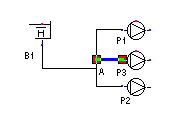
Step 3. Adding connection (slave) from P3 on to connection A
The pictures above show the steps to create a “complex” H-node.
The master and the slave connection line belong to the same H-node. So it doesn’t matter which line you select to edit the properties.
Strings of lines
If you want to connect two components over a long distance it is easier to draw the connection with several shorter lines
First draw the master line that is connected to none or one H-component. Than draw a slave line from the free line end to a second (grid) point. You can attach a second slave line from the free end of the first slave line (and so on).
Deleting master lines
If a line is deleted automatically all lines attached to this line are also deleted. If you do not want this, disconnect the attached lines before delete.
Combining / splitting H-nodes
When one end of a master line is connected to another line, the master line is automatically converted to a slave line. When you disconnect a slave line from another line it is automatically converted to a master line.
2.3.5. Rules for creating a hydraulic model¶
A hydraulic model usually consists of several H-components of different classes connected in a specific way. An example of a hydraulic model is given below.
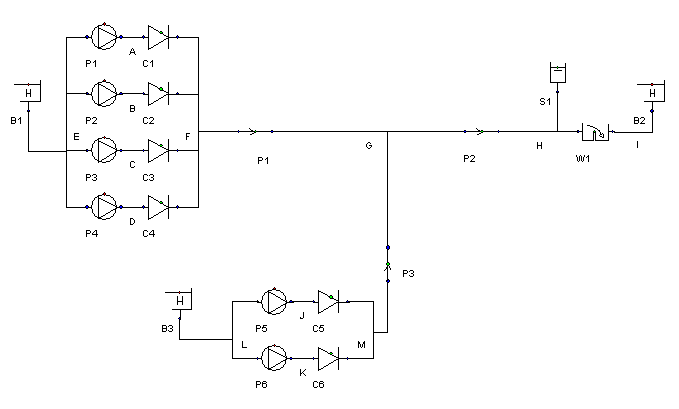
A hydraulic model is built according to a few simple rules. If possible each rule is validated directly and in case of incorrectness a message explains the violation.
Rule 1
A fall-type component has two hydraulic connections: a “FROM” connect point (1) and a “TO” connect point (2) (also called the left-hand side (lhs) and right hand side (rhs)).
The relative position of the two connect points also defines the positive flow direction through the component. This direction is from left to right (FROM –> TO).
Rule 2
A supplier has 1 hydraulic connect point (the FROM).
Note that the positive flow direction at the supplier is from the supplier to the attached H-node.
Rule 3
The number of BOUNDH H-components in the model must be at least one; the number of BOUNDH H-components connected to one connection should be no more than one.
Rule 4
A hydraulic connect point has only 1 incoming or outgoing connection line
A good hydraulic model must be valid (satisfying the four rules above), consistent with the actual piping system and readable. The readability helps to check the consistency of a hydraulic model. For complex systems, however, symbols and straight lines are readily entangled, which makes the model confusing.
As a final remark, it should be noted that building a hydraulic model is by no means a simple “translation” of a real piping system into a computer model following the above-mentioned rules. The rules introduced in this section serve only as a guide for building such a model. Practical skills and engineering judgement are necessary when making a hydraulic model. For example, many details of a real system are actually unimportant for the flow process simulated and can therefore be omitted in the model. This not only saves labour and computer time, but is sometimes also necessary when the system is large and the computer capacities are limited.
An experienced user of WANDA, combined with adequate practical skills and engineering judgement, will find in WANDA a most useful and powerful tool for solving various problems related to transient flow in complex network systems.
2.3.6. Advanced drawing a scheme¶
It is not necessary to place the shape one by one in the diagram and after that to made a connection between them. You can do it in one simple action.
Select the required component from the shape gallery and move the mouse to the existing component. The mouse cursor changes into the connect icon. Now, drag the mouse to the required location and release the button. The program will determine the direction of the new component based on the position of the connected component.
The scheme below has been drawn using the drag and drop feature, and not using flip or rotate.
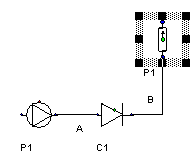
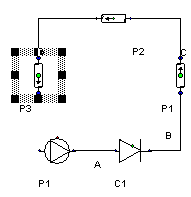
2.3.7. Vector based schematisation¶
The default way to create your scheme is point based: the component is placed in the diagram as defined in the gallery. For GIS oriented diagrams you have to rotate this component. This may be a lot of work.
There is a way to draw the diagram vector based.
First select the component at the shape library you want to draw as vector. Switch on to Vector drawing mode, using the short cut menu.
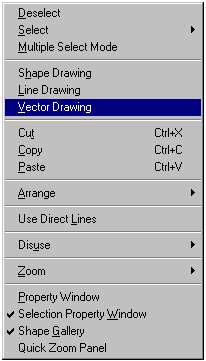
The mouse cursor is changed to a pencil with a line symbol.
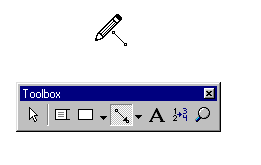
Now you can draw the line. The component selected in the shape library is now automatically inserted in the middle of the new line. The component is automatically rotated to the direction of the line. Click in the shape gallery to select another component. Switch of the vector drawing mode when you are finished.
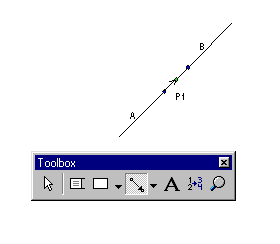
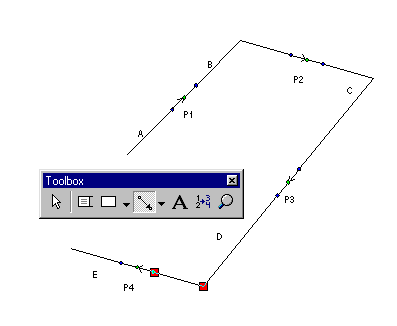
PS: If the component is a supplier it is attached to a free end of the new line.
2.3.8. Aligning routes¶
WANDA 4 offers the possibility to align certain routes or parts of it. This can be useful, e.g. to match the diagram with the actual geographical situation.
See for further detail the Arrange Menu.
2.3.9. Changing the flow definition¶
The direction of the positive flow is depicted in the H-component symbol. The sign of the calculated quantity corresponds with this direction.
If you want to change the positive flow definition, you have to “flip” or rotate the symbol.
Use the menu option Arrange/Flip positive flow direction” to reverse the symbol or the short cut menu.
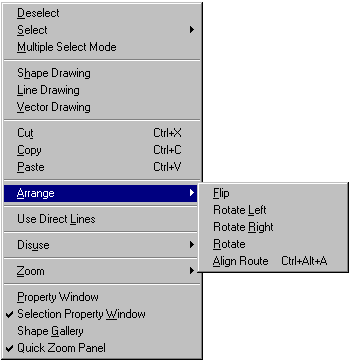
See for further detail the Arrange Menu.
2.3.11. Splitting a diagram¶
To enhance readability of a complex diagram one can use sub-diagrams. A connection line can be split in two using connectors as indicated in the figure below.
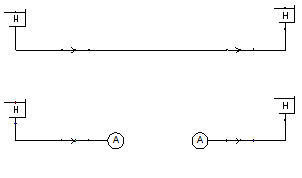
To split the selected master connection line go to “Line and Border” in the Format menu. In the “Format Line” windows select the tab “Arrows and Crossovers”. In the corner left below select the checkbox Connectors. The line is split using connectors with a ‘gap’ in between.
Slave connection lines formerly connecting to the split master line should probably be relocated as they now appear to float freely in the gap between the connectors.

2.4. Property Window¶
2.4.1. Properties of a Component¶
A hydraulic component has several kinds of input and output properties (see Help on Overview of Liquid components). For editing the input properties and viewing the output properties we use the so-called property window.
The Property window applies to individual and groups of selected components. See also: How to use Property Windows.
You see an example of all input and output values of PUMP P1 below.
The property window has his own context sensitive short cut menu which gives you access to common used acts.
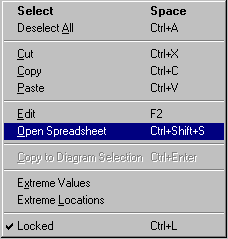
2.4.2. Visibility of properties¶
The content of the property window is for each component different.
See also
The content of the Property Window depends on the operation mode or input values of other properties. An example of mode dependent properties is the component PIPE. In Engineering mode only the length, diameter and wall roughness are required and must be specified; other properties are hidden. In Transient mode the Young’s modulus and wall thickness must be specified in addition. These dependencies reduce the user input to the required minimum number of properties.
The following examples show the Pipe input properties for engineering mode and transient mode:
The contents of the Property Window may also depend on the value of a particular property. As an example the geometry must be specified for the Pipe. The geometry may be specified in several ways: by means of the length, a longitudinal profile or a 3D-geometry. The type of geometry is specified using a list box. The appearance of the Property Window depends on the choice in the listbox ‘Geometry input’. See examples below.
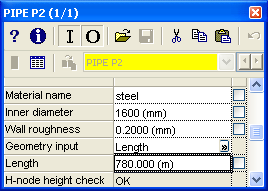
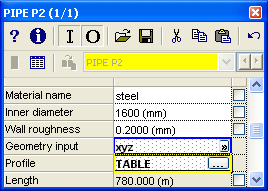
2.4.3. How to use Property Windows¶
The Property Window is one of the most important features in WANDA 4. With this feature it is very easy to view the characteristics of one or more components.
It enables the user to view these characteristics
individually or
in relation to other selected components.
When you select components in your model, its properties and values are automatically displayed in the Property Window. Therefore it is recommended to keep it always open. In this way you can see model, components and properties at a glance.
2.4.4. Example¶
2.4.4.1. Individual components¶
If you select pumps P5 and P6 in the model then the property values for P5 and P6 (individual) are listed in the Property Window:
Inputs and Outputs of P5 and P6 are displayed in the two Property Windows above. The caption shows which component is on top. This is indicated in the diagram by a red circle.
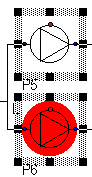
In this way you know at which component you are looking.
2.4.4.2. Font Colours¶
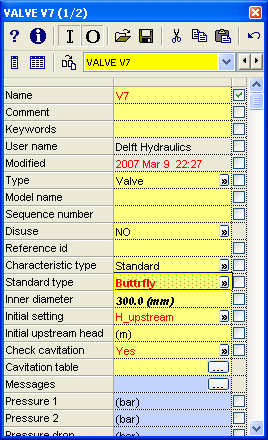
The colours used in the property window have a special meaning.
Values in black-coloured text are identical for the selected components. The edit field ”Type” is the same for both valves for instance.
Values in italic font are linked to extra information. In this example some information is linked to the field “Inner diameter”. For more information on the linking of extra information see “Toolbars” below.
Values in red-coloured text are different for the selected components. Name and Initial setting for V4 and V7 differ from each other.
Values in blue-coloured text are selected or edited. You can (de)select values using the space bar, dragging the mouse in the input area or click in the description area.
Properties with a yellow background are editable properties.
Properties with a grey background are read-only inputs and can’t be modified.
Properties with a lilac background are read-only outputs (calculated) and can’t be modified.
If the output properties have an orange background and a strike-through font, this means that one or more properties in the model are changed and the output is no longer valid anymore. The results are still accessible until you close the changed case.
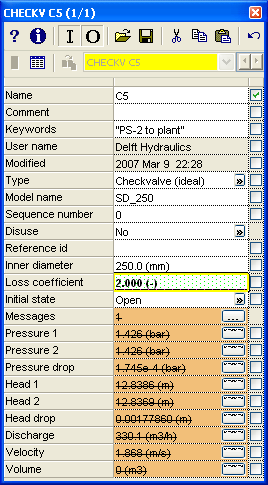
2.4.4.3. Toolbar¶

The buttons in the Toolbar enables you to display the desired information by toggling on or off the buttons and to manage the data in an efficient manner.
All buttons are explained below:
Toggling on Help (or key F1) shows the Wanda Help relevant to the active component. With Shift+F1 the user can add a so-called user-defined help entry in a WordPad file. The question mark gets a yellow background to show that a user defined help entry has been made. In this way the user can extend the standard WANDA Help. It offers the possibility to add tips or tricks related to this component. If the file is saved on a network drive, all other WANDA users in the company can access this information.
Toggling on Information shows two extra information fields. One field that shows what units can be used for this property (see also Units Menu). In this example it shows the available diameter units:
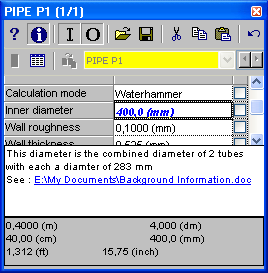
Furthermore, it shows a field with additional information on the selected property. In this case it shows how the Inner diameter of this pipe is calculated: You can also put links to Word-documents or other files in this extra information window. Even pictures are possible. Properties with additional comments can be recognised by a different font (bold+italic). All additional information is saved in the Wanda wdi-file.
Click the right mouse button, for an additional edit menu, to modify your comment:
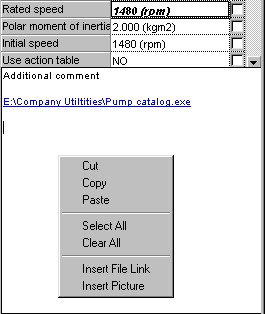
This comment feature is very powerful for quality assurance at project level. Now it is possible to add essential information to each component property. This linked information allows easy access for project reviews, (external) audits, and simple follow-up of projects by colleagues.
This button shows or hides the input properties of the selected component.
This button shows or hides the output properties of the selected component.
Property Template File Management
Open a property template file and apply it to this component, if relevant (see also: Creating your own database system). The retrieved data are displayed in blue.
These buttons enable you to:
Cut the selected (blue) values to the clipboard
Copy the selected (blue) values to the clipboard
Paste the content of the clipboard in this window and thus use it for this component, if applicable (see also: Editing or Synchronising values).
Activating this button shows an overview of the value ranges of all properties of all selected components. This is useful for inspecting the hydraulic model.
Activating this button shows a tabular view of all selected properties of all selected components. This is useful for inspecting and editing into this selection.
This button enables you to Copy (synchronise) the blue-coloured properties to the selected objects in the diagram. See Editing or Synchronising values.
Checkboxes and buttons
Check boxes on the right of the Property Window are used to display or hide the value in the diagram. Component names are displayed by default. You can add other relevant properties to your diagram by checking the boxes. The displayed info remains correct because of the link between the Property Window and the diagram. The property values are put in a text box in the text layer.
For an explanation of the buttons in the edit and output fields, see:
(Use Table): see Tables and tabular views,
(Show Graph): see How to use charts.
2.4.4.4. A group of components¶
The Property window enables you also to see significant values for a group of selected components, by choosing ‘Selection’ in the drop down menu below the toolbar:
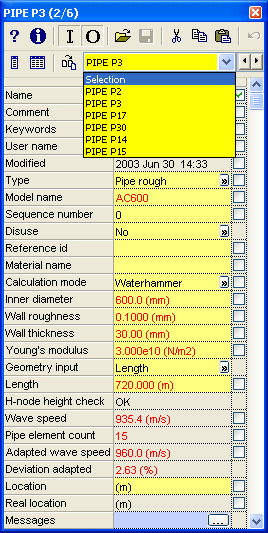
After choosing ‘Selection’ you see the properties in the selection of the components (read-only). If values differ the range of values is shown.
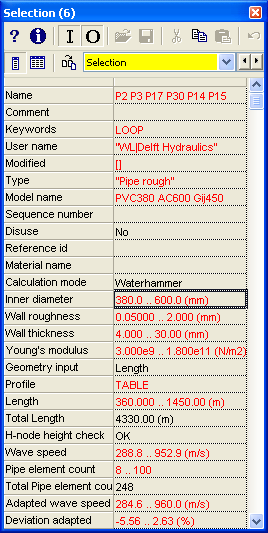
In this example only two components of the same type are shown. Therefore the selection of values is rather transparent. The situation is more complex, if you select more components of various types.
2.4.4.5. Spreadsheet¶
With a spreadsheet you can edit multiple properties of multiple components/nodes.
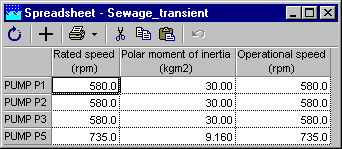
You can copy easily copy/paste selections to Excel/Word.
You can create a spreadsheet by pressing the “grid” button at the Property Window.
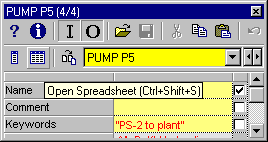
You get a view with the selected objects in the diagram and the selected properties in the Property window.
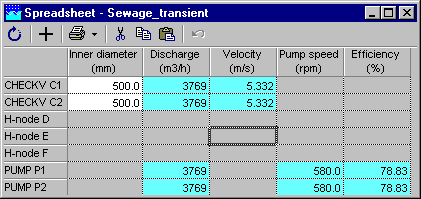
To rotate the spreadsheet press the left button; columns and rows will be exchanged.
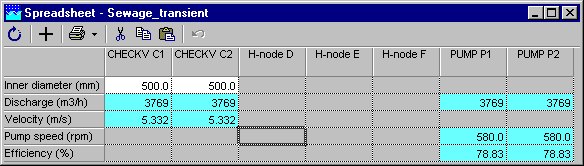

The spreadsheet has his own context sensitive short cut menu. For example, this menu can be used to sort the spreadsheet on an arbitrary column, the selection sequence or a user–defined sequence.
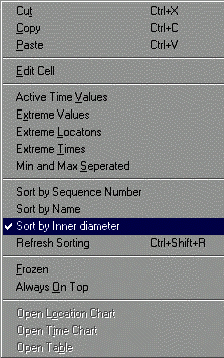
Output ranges, including the corresponding time and location can be viewed in an easy way. The contents of the spreadsheet can be frozen during the edit and simulation session to compare the results with other calculation made within the same session
The tabular view is automatically updated when input or output is changed. When the selection of objects and properties is changed, an existing tabular view keeps unchanged. You can create multiple spreadsheets with different selections.
With the drop down list near the print button, you can set up and create print reports of the spreadsheet.
2.4.4.6. Editing or Synchronising values¶
As discussed the Property Window is the feature to have a detailed look at the components in your model. You can see differences between components immediately, indicated by red text.
Sometimes these differences are unintended. The Synchronise (or copy) feature allows you to solve this problem.
In the property window above you see the properties of pump P5, in a selection with another pump P6. You can see that the (red-coloured) values for the properties differ from P6.
To synchronise one or more altered values for both pumps, you only have to select the values you want to synchronise. To select, drag the mouse or press the space button. Bold text together with a dithered background and a blue outline, indicates which properties have been selected.
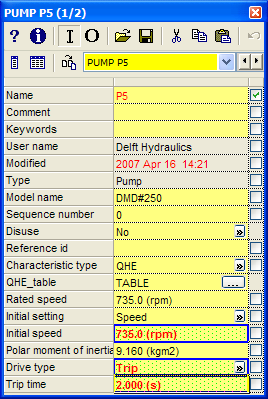
When you click (or shortcut key Ctrl+Enter) the selected values are copied to pump P6.
Note that the output has disappeared from the Property Window after applying Synchronise. The output has to be recalculated, due to a change in input parameters.
2.4.4.7. Tables¶
Pressing opens a table. Some properties, like pump characteristics, pipe profile or action table, are non-scalars but multi-column data series.
The table displays 2 or more input columns. In case of a pump, a read-only column shows you a derived quantity. The edit grid acts as a spreadsheet.
Some type of tables must satisfies certain rules, e.g. a pump capacity curve (QH) is monotonously decreasing; values in first column must be in successive order. If the input doesn’t satisfy the rule the colour becomes red.
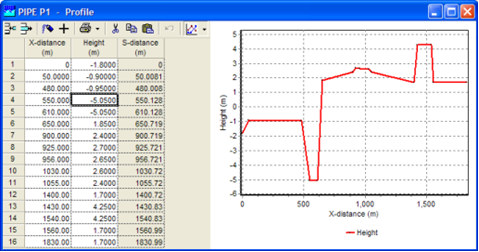
Taskbar
The first two toolbar buttons above, allow you to insert or delete rows in the action table
The ‘plus’ button activates a new window to carry out some simple numerical operations at the selected cells.
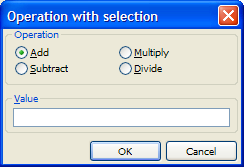
‘Auto fill’ can be used to fill empty cells between two values, using linear interpolation.
The button on the right displays a graph of the table.
See: How to use charts.
Example of pump characteristic table:
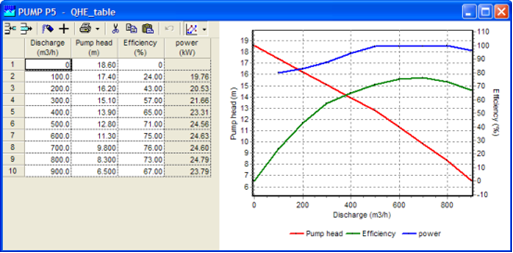
Example of Valve action table
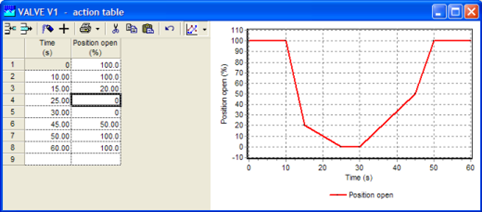
2.5. Selection Builder¶
2.5.1. How to use the Selection Builder¶

In WANDA 4 it is very easy to select single (or groups of) elements. A tool that is very helpful is the Selection Builder (accessed via menu Selection/Selection Builder Window) With this tool you find elements, selected on:
Properties (input and output properties)
At a given time step or during all calculated time steps
Applying a certain operator ( =, <, >, <>, like)
With a given value for the properties.
In this way you can select elements by keywords, inputs and/or outputs. Keywords can apply to any selection (see Add to/ Remove keyword from selection…). You can even build complex queries by applying the Selection Builder several times in succession and by choosing Select or Deselect.
The first 4 operators speak for themselves. The ‘like’ operator is a powerful string-matching operator. The edit field value contains the pattern that is to be matched. This pattern may be a normal keyword, component name etc. Furthermore the pattern may contain one or more of the following special characters:
Character |
Matches |
? |
Any single character |
* |
Zero or more characters |
# |
Single digit (0-9) |
[charlist] |
Any single character in charlist |
[!charlist] |
Any single character not in charlist |
The set of characters in charlist, may contain a hyphen (‘-‘) to specify a range of characters, e.g. [a-k].
Examples
In the screen below we are looking for elements in the model that start with a ‘p’ for the property keyword. (Note that you can use wildcards.)
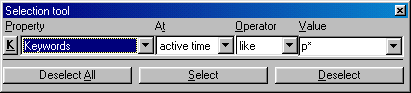
If you want to search on keywords, a dropdown list of available keywords is displayed in the edit value box. We have selected the keyword PS-2 to plant, at the active time, in the example below.
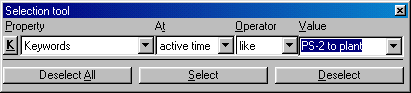
If you want to select all components that have a rated speed of 600 (rpm) or more, you could apply the following selection query. In the diagram, two pumps are now selected.
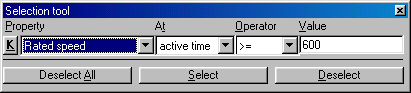
If you click the ‘K’ button, you will go back to searching by keyword.
TipPressing Alt +F7 activates the Selection Builder.
If you press Alt +F7 while a property is selected in the Property Window, this property will be entered in the Selection Builder.
2.6. Using Charts¶
2.6.1. Kinds of charts¶
In WANDA we distinguish three kinds of charts
A chart of an input table: (pump curve, pipe profile, action table etc). The quantity and unit of the X-axis and Y-axis depends on the kind of table.
Time series: This chart contains one or more quantities as a function of time (H(t), Q(t), v(t), etc.). See also Time series.
Location series: Output properties of a pipe can be visualised in a chart as a function of the location (P(x), H(x), Q(x), etc). See also Location series for a single pipe.
Each chart type uses its own default chart template. In these templates the layout of the chart is defined. The user may adapt the templates to personal preferences. More information on managing these templates, see Help function of Deltares Graph Server.
2.6.2. How to use charts¶
If you click the chart button in the Property Window (see How to use Property Windows), a chart of the corresponding output property is displayed. The graph button is part of the output property boxes.
The most important features of charts in WANDA 4 are:
Zoom in on the graph, by drawing a rectangle from left-up to right-down.
Scroll through a zoomed graph by holding the right mouse button.
Change the layout and presentation of the graph by double clicking on the graph or through File menu ‘graph properties’.
Save graph settings in a template, for later use, using the template menu (see also Help Chart server).
Export charts as a Bitmap, Windows Metafile or other formats for use in other applications or documents.
Copy graph data for use in other applications (tab-delimited data, e.g. spreadsheets).
2.6.3. Chart with more series¶
Each time you click the chart-button a new window is opened. If you want to add a series to an existing graph, just press and drag the button into an existing graph. The series is added to this graph.
WANDA allows multiple documents; that means that another case can be opened and that output of more than one case can be drawn in one chart to compare the results of different cases.
2.6.4. Time series¶
Time series are applicable in transient mode only!
All output properties of WANDA objects can be visualised in a chart. This chart contains one or more quantities as a function of time (H(t), Q(t), v(t), etc.).
To create a chart with two or more different output properties, for example the upstream pressure P1 and the discharge Q of a valve, first press the chart button of Pressure 1, then drag the chart button of Discharge into the Pressure chart. The result is displayed below.
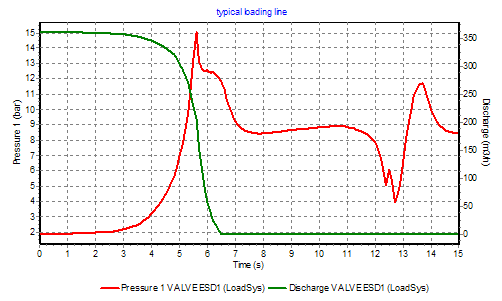
In this way you can also combine different properties of different components.
To create a time series chart with two or more time series of the same output property, first select the objects in the diagram, then press the chart button of one of the selected components. The result is that the output property of all selected components is displayed.
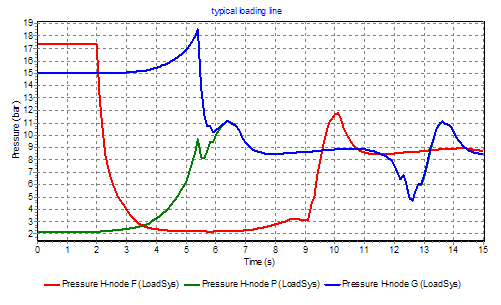
To create a time series at a certain location in a pipe, you have to specify a value in the property field “Location”. The program adapts this location to the nearest calculation node, which is shown in the property field “Real location”. If the Location field is empty, pressing the chart button results in a location chart of the pipe. See also Location series for a single pipe.
2.6.5. Location series for a single pipe¶
The representation of the location chart depends on the mode you are running. In engineering mode the entered profile points are displayed as internal points (see below):
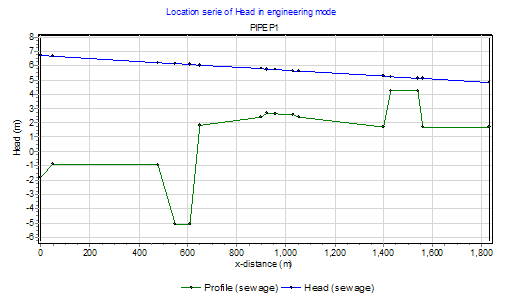
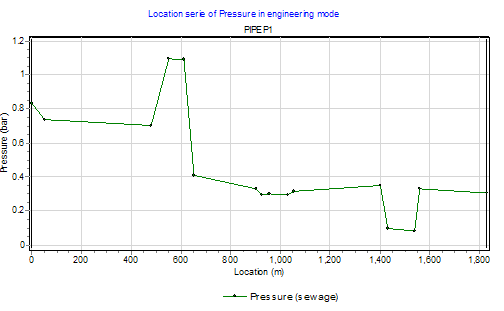
In transient mode the pipe is divided in one or more elements of equal length (based on the wave propagation speed and time step). The output is available in the internal calculation points only (the so-called waterhammer nodes). These waterhammer nodes do not match the profile points. The waterhammer nodes are displayed on the minimum values. The user is strongly recommended to check that the waterhammer nodes cover all relevant high points; decrease the time step if necessary.
In transient mode the chart shows the minimum and maximum values (the envelope) and the values at the current time step. Use the time navigator to analyse the dynamic behaviour (see How to use the Time Navigator). The actual time is displayed in the caption.
The following charts show the same charts as shown in the previous chapter, but now for transient mode:
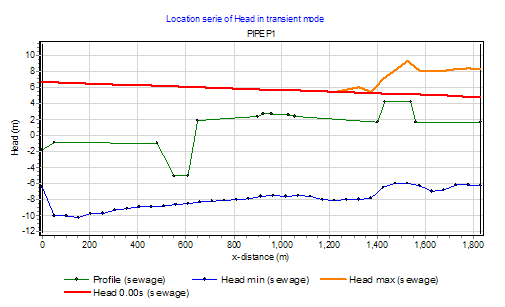
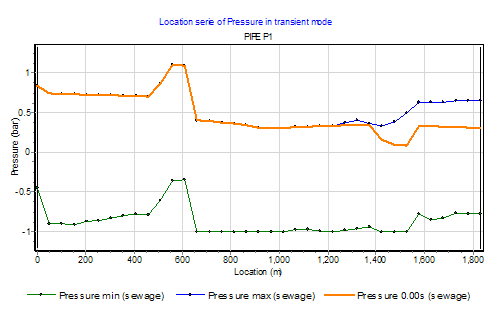
2.6.6. Location series for a route¶
A route is a sequence (string) of selected hydraulic components without a gap. It is not necessary to select the H-components in a route one by one (extend the selection with Shift+Click). The program automatically selects a route by clicking the first component and Ctrl+Shift+Click the last component. For more information of selecting routes see Diagram routes.
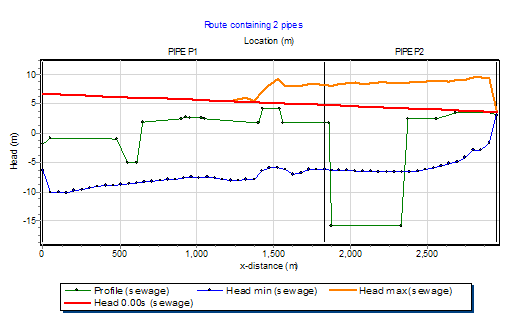
To check if a selection satisfies the route definition, just choose the “Selection” view in the property window (press the A-button). If a chart button is visible at the output properties, the selection defines a route. Only pipe components have a length, other H-components have no length and are not recognised in the chart.
The route function is drawn for the actual time, defined by the Time Navigator (see How to use the Time Navigator. The route creation is the basis for displaying and analysing pressure surge Movies. The actual time is displayed in the caption.
In the chart all pipes are represented in the same flow direction. In a large distribution network it is possible that the positive flow definition is opposite to the current flow. In that case the pipe is represented in flipped position, indicated by a <F>.
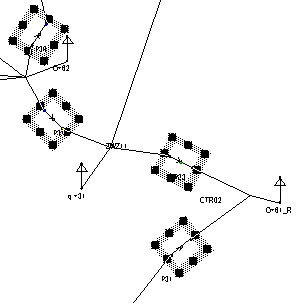
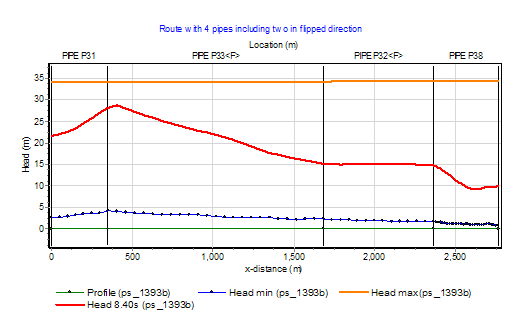
It is possible to display the pressure rating of the pipe in the chart. In the Mode & options menu (Mode and options) a visibility checkbox is available to manage this option. The upper and lower limit values of the pipe are part of the hydraulic input properties of the pipe.
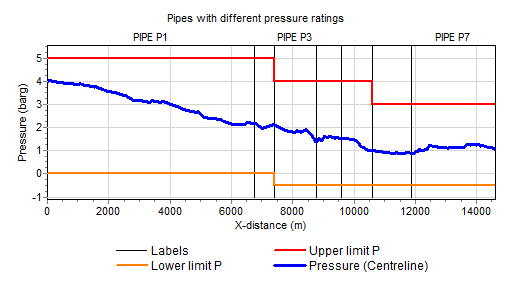
2.6.7. Location axis¶
For a location series, default the horizontal length is used. The user can switch this horizontal length (X-distance) to the spatial distance (S-distance, real length). Especially for vertical pipe sections this may useful. To change this mode, go to the mode & options menu (see Mode and options).
To show the different between both representations the Pressure Head and Pressure charts are given for both axes in case of a pipe bridge (crossing width 10 m, height 6 m).
Bottom axis as X-distance (horizontal):
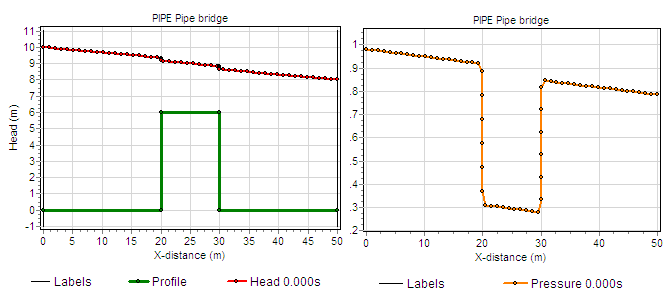
Bottom axis as S-distance (Spatial):
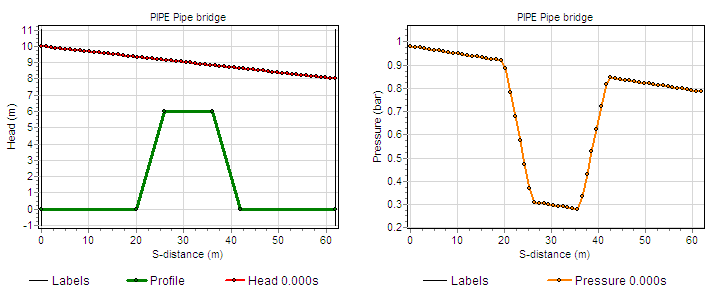
2.6.8. Selection charts¶
Each time you press the chart button in the property window, a new chart window opens. Without closing these windows your screen becomes full within a few moments. It is possible to open one common chart window for a location and one common chart for a time series. Now, when you select an output value, the series is automatically drawn in the chart window. These so-called selection charts are activated via the context sensitive short cut menu (press right mouse button in the property window).
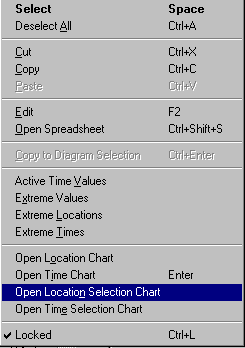
2.6.9. Chart templates¶
The layout of the several kinds of charts are defined in the so-called chart templates. These templates are part of the WANDA delivery. The chart template contains the chart properties, which describe the layout of the chart. If you are not satisfied about the layout, you may edit the chart properties. The modification can be stored in the default template or in a user defined template.
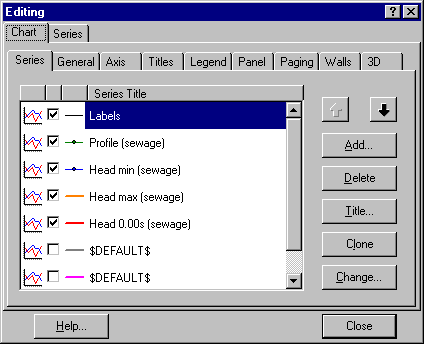
To change the chart properties, double click in the chart or use the menu “file”/chart properties”. All changes are applied directly. To store these settings you must save it into a template. Be aware that the axis title, legend and text headers are variable (text depends on case and kind of property). To maintain these variable text items, the template must be saved in design mode. Choose from the Chart menu “Captions/Absolute”. Then save the template via menu “Template/Save” of activate the Template manager.
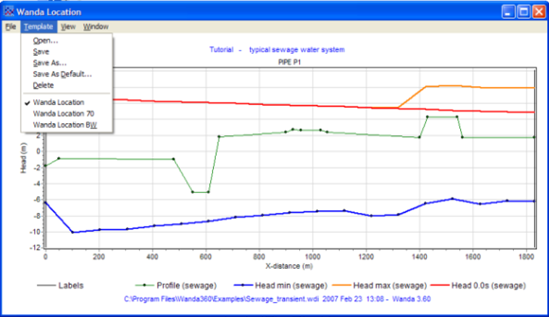
2.8. Creating your own database system¶
2.8.1. Property templates¶
WANDA 4 allows you to create your own set of frequently used settings for all kinds of data. This applies to component properties and specific settings for fluids, accuracy or time parameters.
In this way you can use WANDA 4 the way you want, and adapt the application to your specific use.
Frequently used properties can be stored on disk and re-used. WANDA uses the file system to manage these property templates. An example of such a directory tree is part of the WANDA installation.
For example:
map Fluids contains templates of several kind of fluids
map Pumps contains templates of several kind of pumps
map Pipe sizes contains templates with pipe dimensions for several materials and pressure ranges
map Roughness contains only the roughness property of several kinds of pipe materials.
Important: the delivered property templates are only provided as examples. Deltares not be held responsible for the correctness of the contents.
2.8.1.1. Example: Property window¶
The default fluid window (for Liquid) in WANDA 4, looks like this:
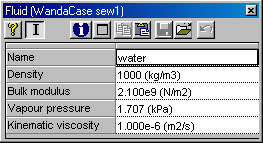
In the model you use, it is possible that you frequently calculate schemes for water of 20 degrees. This means that every time you build a model, you have to adapt the characteristics for water.
In WANDA this problem doesn’t exist because you can create your own template for water of 20 degrees, and store it for later use. All you have to do is give in the characteristics and save them:
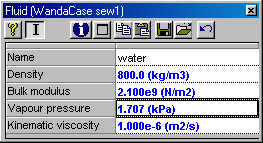
When you click the save button, WANDA asks you for a file name:
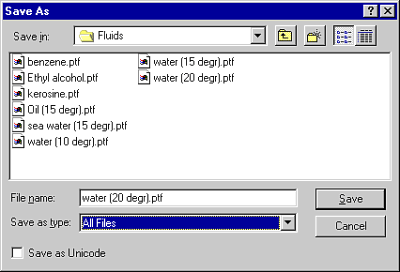
If we open this template in Notepad, it looks like this.
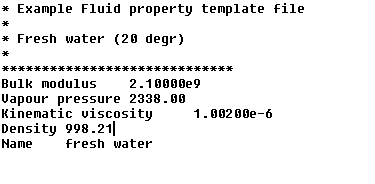
Data is always stored in SI units, but automatically converted if you select another unit system in WANDA.
It is obvious that you can make templates for all kinds of fluids in this way and create your own database system.
The properties are stored in ASCII (text) files with extension “ptf” which stands for Property Template File. We recommend you to extend these files with useful comments.
See next example:
* Source: Catalog Manufacturer XXX
* page II-32a
* Last updated: 1999-09-25 S.O. Mebody Deltares*
Model name HPE 125x110.8
Comment 0.6 MPa SDR176
Material name HPE
Inner diameter 1.108
Wall thickness 0.00710000
Young’s modulus 8.00000e8
If you save component properties to a template, only the selected properties are saved (the blue ones). For the fluid, physical, initial values, user units, all properties shown are saved.
2.9. File Management¶
2.9.1. File management in WANDA 4¶
A complete case study using WANDA produces a set of data files, called case files. The case study is identified by a case name, defined by the user. Case files have the same name as case name but differ by extension. File extensions are administrated by WANDA. This section presents the filename conventions and the way to deal with the data files.
2.9.1.1. Conventions for WANDA file names¶
One set of case files is related to an unique WANDA computation/simulation. To distinguish between different simulations, the user should give a unique case name to each simulation. Case files use the case name as the filename, so that they can be easily identified in the working directory.
The maximum length of a case name including the path (C:…….) is 260 characters (Windows limit). The path and file name may contain blanks.
The general format of filenames is then: “xxxxxxxx.ext” where “xxxxxxxx” is the case name (user dependent), and “.ext” is the extension generated by WANDA. The extensions used, are:
extension |
file type |
wdi |
file for input data |
wdx |
file for iGrafx diagram |
wdo |
file for data generated in both steady and transient computations |
__i |
interface file between the modules STEADY and TRANSIENT |
_sm |
messages (log file) from the module steady-state |
__r |
interface file between the modules TRANSIENT and RESULTS |
_um |
messages (log file) from the module transient-state |
wir |
ascii file containing the input report |
wor |
ascii file containing the output report |
wps |
ascii input file used for parameter run |
wcr |
ascii output file with case compare results |
rtf |
log file, written by closure of case file |
csv |
ascii output file (column separated) with summary output parameter run |
wdd |
ascii file containing the case description text; handy for preview in a file manager |
wmf |
file containing the diagram picture; handy for preview in a file manager |
It is recommended to choose a case name, which contains as much information about the system and process simulated as possible. One may think of, for example, “oilload” or “pumptrip”.
One often needs to make several simulations based on the same hydraulic model. This is possible provided that each simulation has a unique case name. It is advised to administrate the simulations by having serial integer numbers included in the case name, for examples, “pumptrip01”, “pumptrip02”, etc.
2.9.1.2. Important files for backup¶
For backup purposes it is recommended to store at least the WANDA input files in a save place. It is not necessay to store all files because the output files can be generated easily again.
To store the complete input, you need only the “wdi” and “wdx: file.
2.16. Pump Energy¶
2.16.1. Overview Pump Energy module¶
The Pump Energy Module is part of WANDA Engineering. With this module you can calculate the most efficient use of pumps in a pumping station based on a specified delivery pattern and the system characteristic. The program gives you the total energy consumption in a specified period regarding the specified pump operation.
The Pump Energy module is not a separate window but is a combination of a few components. These components are explained in detail in the Help on Overview of Liquid components.
Hydraulics components that must/can be used in Pump Energy are:
PUMP |
the pump model |
PUMPSCEN |
Pump scenario to specify the operation of pumps |
SYSCHAR |
System characteristic |
Q_FREQ |
Discharge Frequency |
Q-PATTRN |
Discharge Pattern |
One or more of these components are placed in the diagram. The module needs only one SYSCHAR and one or more PUMPSCENs and PUMPs. The use of Q_FREQ and Q_PATTRN is optional. These components define the time; without one of these components no energy consumption can be calculated. The system characteristic is a Q-H table defined by the user; it may be retrieved using the System Characteristic module. In that case the curve data must be copied (using the clipboard) from the system characteristic chart to the SYSCHAR input table.
2.16.2. Schematic aspects¶
The figure below shows an example of a diagram to perform a Pump Energy computation.
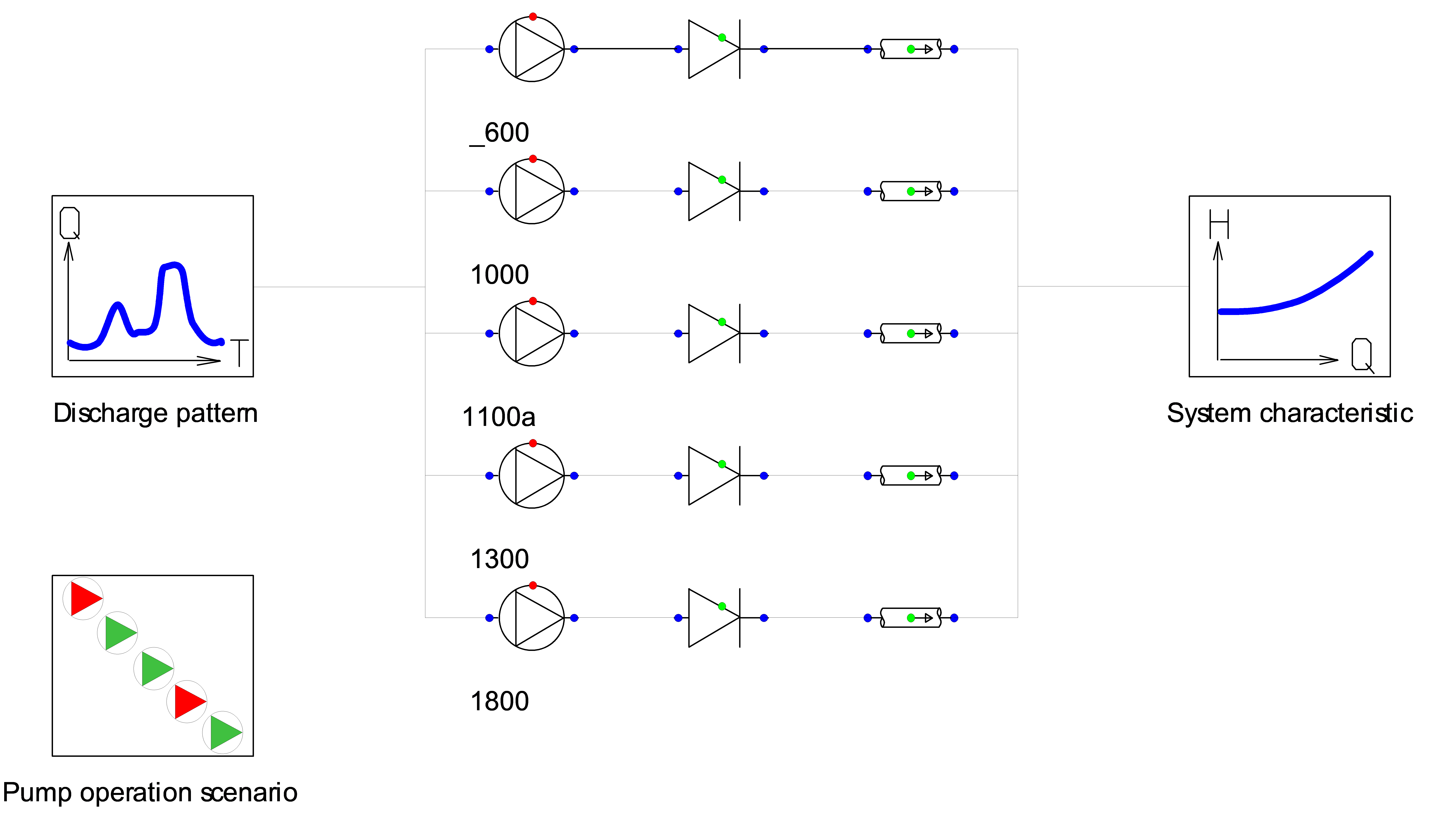
The group of pumps represents the pumping station; other components like valves, checkvalves and pipes may occur in the system but doesn’t have any influence.
Only one (not-disused) SYSCHAR must be present; More than one PUMPSCEN is allowed, so you can compare different scenarios at once. The connections between the different components are not necessary; the PUMPSCEN component carries out the computation based on the specified data of the active PUMP’s, SYSCHAR and (optionally) Q_FREQ/QPATTRN. The computation will be done directly after an input is done; that means that changing a parameter, the new results are directly available.
Inconsistency in the diagram or input is communicated by the message property of PUMPSCEN.
The PumpEnergy components PUMPSCEN, Q_PATTRN, Q_FREQ and SYSCHAR are ignored by the WANDA processes “Steady” and“Unsteady”
The dialog between user and program is done by the diagram: the pumps that must be evaluated are located in the scheme. Only the input fields QHE table and rated speed are necessary, the other values may remain empty.
In the PUMPSCEN component a scenario of operation is defined. The scenario table contains all (not disused) pumps.
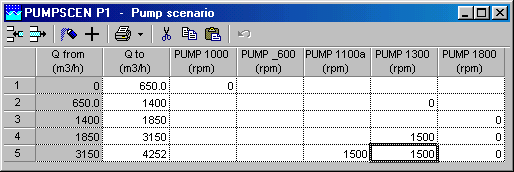
The user has to specify in which discharge range a pump or group of pumps are in operation. The pumps are speed controlled (a “0” is specified) or runs at a fixed speed (the concerning speed is specified). In above example the first 3 stages are operated with variable speed pumps, 1 different pump for each different case. The next stages are operated with one or two pumps at fixed speed and one at variable speed.
The PumpEnergy module calculates for the whole range of discharges the efficiency and power of each pump. In case of variable speed pumps, the necessary speed is calculated to satisfy the duty point according the system characteristic. All important pump properties, like discharge, head, speed, efficiency and power, can be visualised.
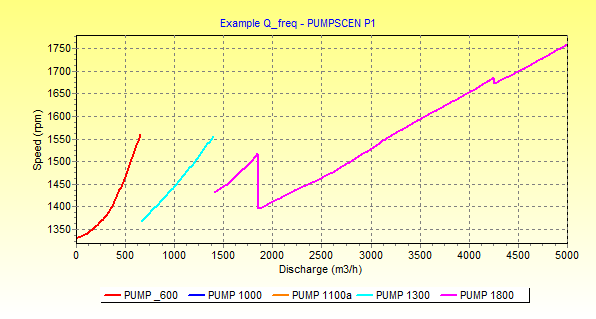
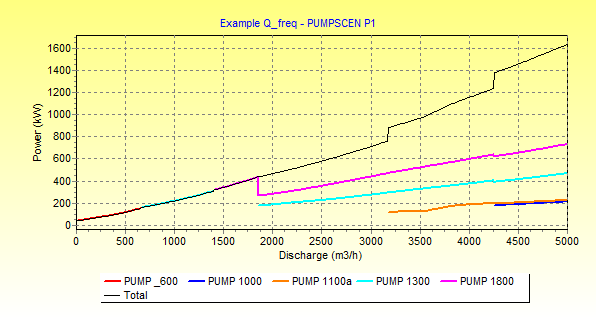
If we know how many hours the pumps operate, the energy consumption can be determined.
The time aspect can be specified in two different ways:
a histogram annotation that tell us how many hours a certain discharge is delivered in a certain period (Q_FREQ)
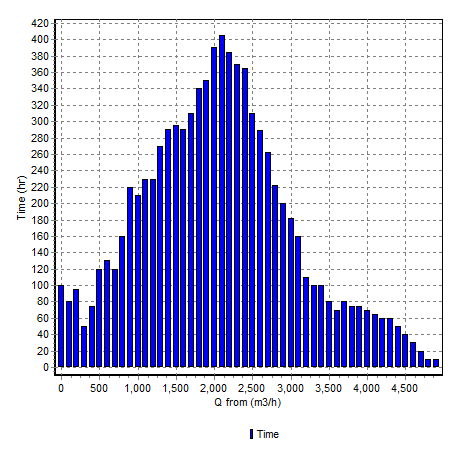
a discharge pattern as function of time (Q_ PATTRN)
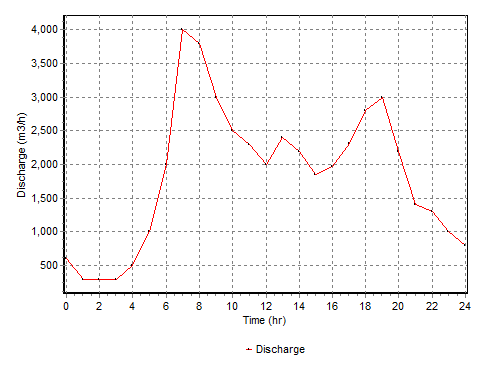
The energy consumption is displayed in the scenario table and can be visualised in a chart
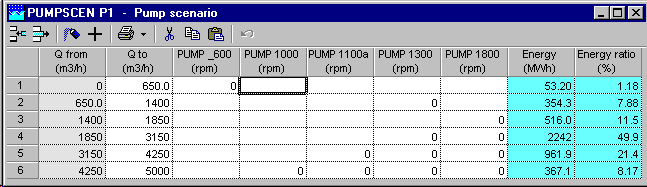
More information about the individual Pump Energy components is explained in the Help on Overview of Liquid components.
2.17. Tips for WANDA 4 users¶
2.17.1. General tips¶
Read the manual.
Always make a (temporary) local copy of a Wanda case stored on a network server or removable drive. Data is loaded dynamically so the access time determines the speed of Wanda. The access time of a local drive is about 100 times faster.
Use the context sensitive menu (right mouse click) in the diagram and property window to get fast access to frequently used options.
You can open a Wanda file from a file manager by double clicking the wdi-file or dragging a wdx-file into the Wanda diagram window.
You also can drag a file to the windows taskbar. Keep the mouse button down until Wanda becomes visible and move the dragged file in the diagram window.
You can use your favourite text editor (Messages, Reports) by associating the txt-extension to your favourite text editor. (‘View.Options.File types’ menu item in the windows file explorer).
Use the same model name for components that share the same specifications (properties).
Use keywords to group a set of Components.
The information in every window reflects the current situation. You don’t have to re-open windows to update them.
If you are not interested in the output at every single time step check the ‘Show Extremes’ option in the Model menu.
Press F11 to switch the focus between the property window and the diagram window.
Wanda works best at a resolution of 1280x1024 and a 19” monitor or better.
Sometimes the diagram doesn’t become visible when you click the taskbar. Right click the Wanda button at the taskbar and choose restore.
You can resume transient with a different output increment.
Make property templates with fluids that you use frequently.
You can delete the wdo-files of cases to create more disk space. When you delete the wdo file of a case only the output is deleted. If you send a case by mail create a zip file with the wdi and wdx file. These three files are the only files needed.
Learning the keyboard and mouse shortcuts will save time when you are using Wanda frequently.
If you have additional tips lets us know.
2.17.2. Shape libraries¶
You can customise the Wanda Hydraulic and Wanda Control shape library.
You can add extra custom shape libraries.
DON’T DRAG WANDA COMPONENTS FROM THE DIAGRAM TO THE SHAPE LIBRARY.
You can copy shapes from one shape library to another. Use the right mouse button to cut/paste.
Copy shapes between shape libraries one by one. If you don’t, Wanda will crash due a bug in iGrafx.
It’s easier to collapse the gallery than closing the gallery. Use the button ‘>’ left from the ‘X’
You can resize the buttons in the gallery (shape libraries) by moving the right-down corner of a single button.
2.17.3. Diagram general¶
The mouse cursor indicates what happens when you click (Selecting, Moving, Dragging a line, Inserting a new component).
Hold the SHIFT-key down while clicking an object to extend a selection by a single object.
Hold the SHIFT-key down while clicking a selected object to shrink the selection by a single object.
You can drag a selection rectangle to select multiple objects at once.
You can extend a selection by multiple objects at once by dragging a rectangle while the SHIFT-key is down.
If you change the line style / weight / colour while no objects are selected the style is applied for new lines and shapes.
You can visualise a property in the diagram by clicking its checkbox in the property window.
If you toggle the menu item ‘show extremes’ the output properties in the diagram are also changed (delay 3 seconds).
If you move the slider in the time navigator the output properties in the diagram are also changed (delay 3 seconds).
Use a postscript printer driver when the diagram or chart is not printed correctly. (HP delivers also a postscript driver for all it’s laser printers).
Right click at a component or connection to popup extra property windows.
Deselect all objects before printing to prevent red circles behind objects.
Before you copy the diagram selection to another application (e.g. MS Word) first press the ‘A’ button in the property window. This prevents that a red circle behind a component is also copied.
Some Nvidia video drivers don’t work properly when using iGrafx professional. Wanda crashes during starting or directly after adding a component. Download the newest video driver from the Internet. It’s still possible that background pictures hide the diagram partly. Use a separate layer for the pictures and hide this layer during editing.
By pressing CTRL+F6 you can quickly switch between open diagrams.
To navigate in large scheme’s, use the split window mode. The upper part is used for navigation, the lower part is used for editing.
2.17.4. Diagram editing¶
If you are dragging a selection you can cancel this operation by pressing the escape button before releasing the mouse button.
Hold the CTRL-key down if you want to copy a selection instead of moving a selection.
You can draw components like vectors (Wanda 2 functionality). Select from the shape library the component type you want to draw. Press the shift key and keep it down. Right click the diagram background to switch to the line draw mode. Draw a line. The selected component in the shape library is now automatically inserted in the middle of the new line. The H-nodes (connection lines) at both sides (only upstream side in case of a supplier type) are automatically generated. When you are finished with vector drawings you can release the shift button.
You can hide/unhide the grid dots with the sub menu “Grid” in the “Arrange” menu.
Editing is easier when you first ‘snap to grid’ all components. If you convert a Wanda 2 case the diagram size is reduced with 25 percent. Due to this reducing the objects are not ‘snapped to grid’.
If you want to connect a connection line in the middle of another connection line which is very short (less than 1 cm), the green blinking connect point snaps automatically to the end points. Accept this location while the WANDA program moves it to the centre of the line.
If you want to move a text (e.g. name) of a component/node first select the tab “Text” in the diagram window.
Don’t move a selection to another document.
Copy the selection first and delete the original selection afterwards.
You can align components by using the blue rectangle. When you move a component across another component this component is marked with a blue rectangle. Keep the mouse button down and move the component to the wanted location. When you release the mouse button the component is snapped to the position that’s exactly aligned with the blue marked component.
You can shift + right-mouse-click at the diagram background instead of pressing the line tool button. Press twice to toggle between direct line and right angle line
You can ctrl + right-mouse-click at the diagram background instead of pressing the last selected shape at the shape library.
By adding extra vertexes to a connection line you can route the line to another path. You can add extra vertexes to connection lines by pressing the right-mouse button while you hold the SHIFT-key down.
If the diagram isn’t displayed correctly or the selection isn’t the same as in the property window press F5 (Refresh) while the diagram is active.
2.17.5. Diagram layers¶
Use a separate layer for pictures (backgrounds). You can quickly hide this layer to increase the scroll/zoom speed and reduce flickering (layer manager, activated by right click at layer tab). The background must be the first in the list (use move up button), otherwise the components are not visible.
Move (a group of) disused components to a different layer. You can toggle the printable option when you right-click the tab. When the option is unchecked the layer is not visible when you print the diagram.
If you want to edit multiple layers choose edit all layers and lock the layers you don’t want to edit.
Right click at a layer tab to see a context menu. With this menu it is easy, among other things, to hide and unhide layers. It’s important that the layer-tab that you want to hide is not active.
2.17.6. Diagram routes¶
A route is an unambiguous and continues sequence of H-components; this route can be specified with a keyword.
You don’t have to select all the component in your route one by one. Select the first component in your route. Now select the last component in your route while holding the Ctrl and Shift key down. The other components and connections in the route are now automatically added to the selection. It’s important that the components are connected before you select the route.
If the route Wanda chooses isn’t the way you had in mind you can select extra components before you select the last component by Ctrl+Shift+Click. Now Wanda is forced to choose a certain path. Keep the Shift key down while you select the extra components.
Use the ‘align route’ menu option or (CTRL+ALT+A) to align a route in a fast way to another direction. First move component A to the wanted position, then move component Z to the wanted position. Choose ‘align route’ to redirect all components between A and Z in a straight way.
2.17.7. Property windows¶
If you select multiple components/nodes you can inspect multiple properties by pressing the ”range” or “spreadsheet” button in the property window.
To select/deselect properties in a property window, press the space bar, click at the description or drag the mouse in the input field.
You can drag/drop selected properties from one property window to another property window.
Every component/node also has hidden properties. With the hidden properties you can see the connectivity used by steady and transient. To unhide the invisible properties press the pause key while a property window is active (may be useful in case of ‘strange’ problems).
If you are editing a text property you can insert a line break by pressing ALT+ENTER (same way as in Excel).
You can quickly move to a property in the property window by pressing CTRL+ALT+”First character property name”.
If you want to edit a part of a property value first press F2 or enter to become in edit mode.
You can open a table or chart window by pressing enter at the particular property.
Use the menu items ‘Add keyword to selection’ and ‘Remove keyword from selection’ to update the keyword list when you have a multiple selection.
Export your frequently used properties of components to property templates. Now you can easily reuse components between cases (or colleagues).
You can load a property template file from the file manager by dragging the file into the info/unit section of a property window (I-button must be pressed).
You can see the Wanda help while editing the properties by setting the online help ‘always on top’.
2.17.8. Tables and tabular views¶
To show a tabular view, select one or more properties (marked as blue) in the property window and press the ”spreadsheet” button.
You can print a table or tabular view by a right double click at the grid. An Excel like window appears. Choose ‘Page setup.’ in the file menu to fit the print to n by m pages (landscape or portrait).
While you are defining the pipe profiles of the pipes in a route you can open the Head chart to see the profile of the complete route. This chart is updated while you are changing a pipe profile in the route.
The contents of the spreadsheet can be copied to Excel using the clipboard.
If copying data between Wanda and Excel fails, check the regional settings. The decimal symbol must be set to “.” (dot).
You can open multiple spreadsheets at the same or at different cases.
To change rows and columns, press the rotate button.
When you press CTRL+F4 the window closes and the focus returns to the property window.
2.17.9. Charts¶
Use the most recent printer driver when charts are not printed correctly.
You can drag/drop chart-series buttons (also from different cases) to a single chart window (also when a movie is playing).
Use an applicable short name if you have a multiple case chart. The short name is added between brackets to the series title. You can change the short name of a case in the description window.
Make you own chart templates if you are not satisfied with the default graph settings.
There are four groups of templates: Time series templates, Location templates, table templates and system characteristic templates. Templates can be shared or copied to another group by copying a local template to a global template.
Before saving a chart template first check the ‘captions.absolute’ menu item. You see now the quotes that are not converted to keywords. These quotes are saved absolute to the template. You can choose ‘Reset to default’ to remove all absolute quotes.
You can see multiple location series at once (Route) when clicking a chart button. First make a multiple selection of pipes. All the pipes in a selection must have the same flow direction. Also select components between selected pipes.
You can see multiple time chart series lines at once when you click a chart button. First make a multiple selection of components with the time series you want to see.
Fill the location property if you want to see pipe time chart series instead of pipe location chart series.
- Use the right mouse click to open a “selection chart window”. This is a global window wherein each selected property chart is drawn.The advantage is that now only one chart window is used for all time series and one for all location series.
You can drag a chart button to a chart that already has that location property. This location series is frozen at the active time step. Also frozen series are automatically updated when you run steady/transient again.
You can quickly zoom into a chart by dragging a rectangle from left to right.
You can quickly undo zoom by dragging from right to left.
You can scroll the chart down/up and left/right by moving the mouse while the right mouse button is pressed.
Line patterns don’t work fine if the series points are close together.
2.17.11. Selection builder¶
If you don’t specify a value and using the ‘=’ operator Wanda searches for empty/missing values.
If you specify a ‘*’ as value and using the ‘like’ or ‘=’ operator Wanda searches for every value.
You can use the hidden colour property to select all objects with the same colour.
2.18. Frequently asked questions¶
2.18.1. Manage files¶
Questions |
Answers |
Which files are necessary for backup purposes |
All input of the case is stored in the wdi and wdx file; all other files can be generated again performing the calculation. |
I can not save my WANDA case |
You are probably viewing a WANDA case with components that are not part of your license. You can only save cases that can be built with your license. Press F10 to select the unlicensed components. |
2.18.2. Gallery/Shape library¶
Questions |
Answers |
The gallery is not visible |
Go to menu “view” and mark “Gallery” as visible, or activate the right mouse click menu and check “shape gallery” |
One of the shape libraries is not available in the gallery Hydraulic (no tab visible) |
At the gallery tabs, click the right mouse button; choose “open palette” and select form the group “Wanda components” the required subject |
The component tooltip text is partially not visible, it disappears behind the property window |
The property window is always “on top”. Move the gallery window to the left side of the diagram. |
2.18.3. Route¶
Questions |
Answers |
How can I create routes? |
There are several ways to select a route (a route is a concatenation of 2 or more H-components). A very fast way is click first H-component followed by CTRL-click of last required H-component. WANDA selects the shortest route. If a particular H-component must be part of the route, add them to the selection before creating the route. |
See also: Select route between selected components or use the short cut menu.
2.18.4. Diagram / Layers¶
Questions |
Answers |
It is not possible to move the text labels in the diagram. |
The model is built in different layers. Choose the “text” layer tab at the bottom of your WANDA window to change the position/font/size of the text. |
How can I put a map as wallpaper to my diagram? |
On the Arrange menu, point to Layers, and click Add Layer. The new layer is added in front of the current layer and becomes the new current layer. The wallpaper layer must be moved up to the top On the Insert menu, point to Picture and specify a bitmap picture from file Resize the picture to the desired size |
How can I rotate or flip a component |
Press the right mouse button in the diagram and choose “Arrange”, or use the “Arrange” option from the menu bar. Flip and rotate buttons can be made visible via “view/toolbars” menu, check the draw toolbar. |
I want to draw a H-component in another direction than from left to right. Is that possible without using the flip/rotate? |
In vector line mode you can draw a H-component including its connection lines (H-nodes) in one movement. From the diagram short cut menu choose “Vector drawing”. Draw a line and the active H-component is placed in the centre of the line. Press Esc-key to leave the vector mode or choose from the short cut menu another mode. Another way to draw a component in a other (straight) connection is as follows: Draw the new component starting at an existing component by dragging the mouse. The new component is automatically arranged in the direction of the connection line drawn. |
Can I change the connection line type afterwards? |
Yes, a direct line can be changed to right angle line or just the other way round. A curved line can changed in a direct line or right angle line only |
2.18.5. Property window¶
Questions |
Answers |
What is the difference between the properties “Model name”, “Comment” and “Keyword”? |
In fact all of them are additional strings to describe the H-component. Model name and Keyword have particular intentions. Model name is introduced to define a particular identification of the H-component, e.g.: serial number, product ID, manufacturer name. In the next WANDA version this name will be used as default name for the property template file, when properties are exported or imported. Cases built with WANDA 1 and 2 uses the so-called common spec labels. These labels (used for data sharing) are replaced by a more generic data sharing concept; see also Properties of a Component. Common labels are assigned to the property “Model name”. The “Comment” field has no special meaning; use this for additional remarks. The “Keywords” field is used for quick selection. A H-component may have more than 1 keyword. Keywords are added and removed using the “Selection” menu; see Selection builder. Use keywords for Route definitions, groups of components (Pump station, High Pressure System etc); see Selection builder. |
2.18.6. Charts¶
Questions |
Answers |
How can I show more time series of the same quantity in 1 chart? |
Select first the wanted components (or H-nodes), then push the chart button of the wanted quantity. All series of the selected components are drawn in 1 time If you want to add new series, press the chart button and drag it into the existing chart. Release the mouse button and the new series will be added into the chart. |
Is it possible to show more series of different quantities in 1 chart? |
Yes, create a new chart by pressing the chart button. This property quantity is drawn at the left axis. Drag the chart button of the second quantity into the chart. This quantity is drawn at the right axis. It is not possible to have more than 2 different quantities in 1 chart. |
Is it possible to show more series of different calculations? |
Yes, create a new chart by pressing the chart button in case 1. Open case 2 and select the wanted component. Drag the chart button of the wanted property into the chart. To distinguish both series, use “legend name” from the menu “model/description window” |
How can I remove or change format from the footer text from the chart (in the footer text the case file and edit/run time is displayed) |
Choose from the model menu “Description window” Select form field “Chart footer” the required display text . |
How can I change the layout of the chart? |
Double click in the chart or choose menu “file/chart properties”. You become in the edit window at which all elements of the chart can be changed. The changed settings can be changed. See next question. |
How can I save the changed layout settings of a chart? |
To store these settings you must save it into a template. Choose from the Chart menu “Template”.followed by Save, Save As. or Save As Default. Using this Template menu you can switch between several layouts |
2.19. Important keys and shortcuts¶
2.19.1. Windows general¶
2.19.1.1. Keyboard¶
Ctrl + F4 |
Close document window |
Ctrl + F6 |
Next document window |
Alt + F4 |
Exit application |
Ctrl + Shift + N |
New |
Ctrl + O |
Open |
Ctrl + S |
Save |
F12 |
Save as |
Ctrl + P |
|
Ctrl + A |
Select all |
Ctrl + X |
Cut |
Ctrl + C |
Copy |
Ctrl + V |
Paste |
Ctrl + Z |
Undo |
Ctrl + Y |
Redo |
F2 |
Edit Text |
Shift + F10 |
Popup context menu (right click menu) You can also the special button between the right alt and ctrl keys |
2.19.1.2. Mouse¶
Ctrl + drag |
Copy |
Shift + drag rectangle |
Select and keep old selection |
Click |
Select |
Shift + click |
Select and keep old selection |
Right Click |
Popup Context Sensitive Menu |
2.19.2. IGrafx Diagram¶
2.19.2.1. Keyboard¶
Ctrl + Shift + 4 |
Align Top |
Ctrl + Shift + 6 |
Align Middle |
Ctrl + Shift + 8 |
Align Bottom |
Ctrl + Shift + 3 |
Align Left |
Ctrl + Shift + 5 |
Align Center |
Ctrl + Shift + 7 |
Align Right |
F5 |
Redraw diagram |
F2 |
Start (editing) text |
F4 |
Focus window on the currently selected object |
F6 |
Note window |
F7 |
Spelling |
F9 |
Open shape library |
Ctrl + U |
Underline |
Ctrl + I |
Italic |
Ctrl + B |
Bold |
Ctrl + D |
Format text |
Ctrl + F9 |
Move (selected objects) back one layer |
Ctrl + F10 |
Move (selected objects) forward one layer |
2.19.2.2. Mouse (click at background, not at object)¶
Click |
Deselect all objects |
Ctrl + right click |
Activate shape insert mode |
Shift + right click |
Activate connect line insert mode. Change connect line mode (direct, rectangle) when line mode is already active |
Shift + line draw |
Add active shape including 2 connect lines (keep down while drawing a line). This is called vector-based schematisation. |
Drag rectangle |
Main Panel: Select objects in rectangle Quick Zoom Panel: Zoom to rectangle |
Shift + Drag rectangle |
Select objects in rectangle and keep selection |
Alt + Right click |
Best fit all (Zoom out) |
2.19.3. Wanda diagram specific¶
2.19.3.1. Keyboard¶
F10 |
Select first invalid component |
Tab |
Toggle focus between diagram and selection property window |
Ctrl + M |
Activate mode / option window |
Ctrl + T |
Activate time navigator |
Shift + F9 |
Run steady |
Shift + Tab Shift + F11 |
Hide/unhide selection property window |
Alt + F3 |
Activate description window |
Alt + F5 |
Show system characteristics dialog |
Alt + F7 |
Activate selection builder window |
Alt + F9 |
Run transient (and steady when required) |
Ctrl+Shift+F10 |
Select all components with warnings or errors |
Ctrl+Shift+L |
Activate Property Labels Window |
Ctrl + Alt + F |
Flip positive flow definition |
Ctrl + Alt + I |
Show initial values window |
Ctrl + Alt + T |
Activate time parameters window |
Ctrl + Alt + F9 |
Stop / resume transient |
2.19.3.2. Mouse (click at shape/line)¶
Drag rectangle |
Main Diagram Panel: Select objects in rectangle Quick Zoom Panel: Zoom to objects in rectangle |
Ctrl + Shift + click |
Select shape and select route between selected shapes |
Right click |
Activate relevant menu options |
2.19.4. Property window¶
2.19.4.1. Keyboard¶
F10 |
Select first invalid component |
F11 |
Toggle focus between diagram and selection property window |
Ctrl + S |
Save selected properties to file |
Ctrl + O |
Open properties file |
Ctrl + C |
Copy selected properties to clipboard |
Ctrl + V |
Paste selected properties from clipboard |
Ctrl + R |
Toggle Overall view of selection |
Ctrl + I |
Show/Hide Info/Unit Pane |
Ctrl + Shift + I |
Show/Hide Input |
Ctrl + Shift + O |
Show/Hide Output |
Ctrl + Shift + S |
Activate Spreadsheet Window |
Ctrl + Enter |
Synchronise button |
Page Down |
Jump to next selected component in selection/route |
Page Up |
Jump to previous selected component in selection/route |
F4 |
Drop down yellow selection list box |
Space |
Select/deselect property |
Shift + arrow down |
Select/deselect property |
Alt + Ctrl + letter |
Quick search for a property name (starting with specified letter) |
Letter |
Start editing property (overwrite existing value). Dropdown list and jump to value starting with specified letter |
F2/enter |
Start editing property (change text instead of overwrite text) / Open a table / Open a chart / Dropdown value list |
Enter |
Stop editing a (text) property / Apply dropdown value |
Esc |
Cancel editing a property |
Alt + enter |
Insert manual line break when editing a text property |
Esc |
Hide special property window (e.g. Fluid) |
+, /, * |
Arithmetic operation with active cell |
Pause |
Show/Hide invisible properties |
2.19.4.2. Mouse¶
Double click |
Edit / Open table / Open chart |
Click at property name |
Select / deselect property |
Drag rectangle |
Select / deselect properties /checkboxes in rectangle |
Drag button |
You can drag a chart button to an existing chart to add series |
Right click |
Activate relevant menu options |
2.19.5. Table Windows¶
2.19.5.1. Keyboard¶
Ctrl + Enter |
Insert Row |
Ctrl + Delete |
Delete Row |
+, /, * |
Arithmetic operation with selected cells |
Ctrl + P |
Popup print menu |
Ctrl + G |
Show/Hide chart |
Ctrl + E |
Chart Setting |
Ctrl + T |
Chart templates |
Ctrl + Shift + Space |
Select column |
Shift + Space |
Select row |
Ctrl + A |
Select All / Deselect All |
Esc |
Close table window Cancel editing a cell |
Shift + Arrow keys |
Select cells |
F2 |
Edit cell |
2.19.5.2. Mouse¶
Double click |
Edit cell / Open table / Open chart |
Drag rectangle |
Select cells |
Right click |
Activate relevant menu options |
2.19.6. Spreadsheet windows¶
2.19.6.1. Keyboard¶
Ctrl + R |
Transpose, Swap rows and columns |
Enter |
Open table / Open chart |
+, /, * |
Arithmetic operation with selected cells |
Ctrl + P |
Popup print menu |
Ctrl + Shift + Space |
Select column |
Shift + Space |
Select row |
Ctrl + A |
Select All / Deselect All |
Esc |
Close spreadsheet window Cancel editing a cell |
Shift + Arrow keys |
Select cells |
F2 |
Edit cell |
2.19.6.2. Mouse¶
Double click |
Edit cell / Open table / Open chart |
Drag rectangle |
Select cells |
Right click |
Activate relevant menu options |