5.35. PIDSS_N¶

Purpose
To achieve a certain set value by adjusting a controlled variable of a hydraulic component, based on the difference between the input value and the set value. The PIDSS_N component includes an ON/OFF switch and is therefore similar to the PIDSS component, except that the error and output can be normalized. The component is mainly used for pump sumps in sewage systems.
Procedure
The Proportional, Integrate, Differentiate Start/Stop (PIDSS_N) component requires a minimum of two input signals: The first ‘input signal’ is used to compute the output signal. The second ‘switch value’ signal is used to determine whether to switch the PIDSS_N component ON or OFF.
The PIDSS_N component has four states: OFF, STARTING, ON and STOPPING (See Figure 4). Assuming the initial state is OFF, at the moment the input ‘switch value’ signal exceeds the ‘switch ON’ level, the state will change to STARTING. The output signal will then change linearly in time (bound by the ‘ramp value’) from the ‘output value when OFF’ to the ‘output start value’. The state then changes to ON.
During the first part of the ON state the output remains equal to the ‘output start value’ for a duration specified by the ‘stabilize time’. The second part of the ON state is the CONTROLLING part of the PIDSS_N component. If the input ‘switch value’ drops below the ‘switch OFF’ level the state will change to STOPPING. In this state the output value will decrease linearly from the ‘lower bound value’ to the ‘output value when OFF’, bound by the ‘ramp value’. Thereafter the state will revert to OFF.
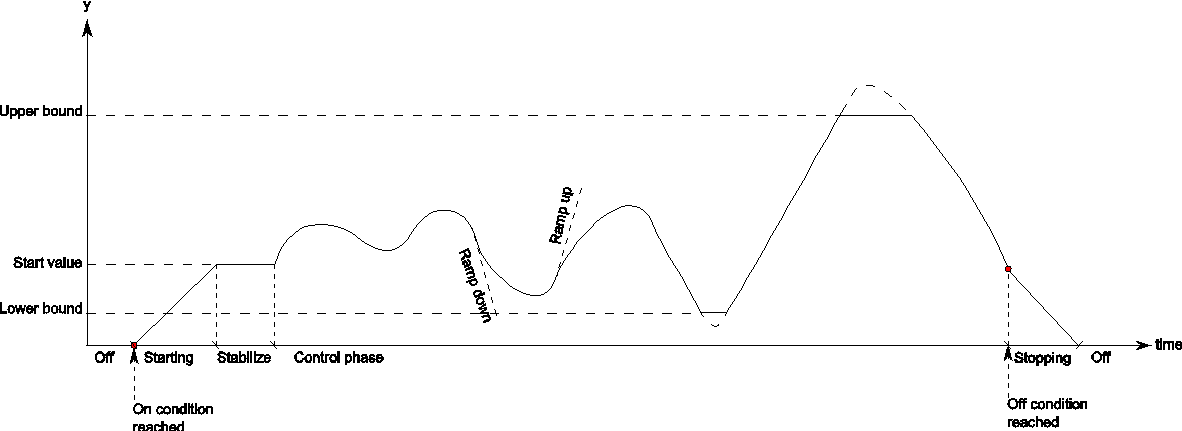
Figure 7: PIDSS_N operation
The Proportional, Integrate, Differentiate Normalized (PIDSS_N) component computes for each sample period Δt the error ε between an input signal x[n] and a set value xset:
and upper bound values:
The unscaled output signal is computed by
Proportioning:
Integrating:
or Differentiating the normalized error:
where cp is the “gain” (whose units are determined by the units of the output signal), ci is the “integration time” (time units), cd is the “differentiation time” (time units), Δt is the sample time-step and [n-1] denotes the previous sample. The equations above can be combined to give an unscaled output signal, which is either:
Proportional (P):
Proportional and Integrated (PI):
or Proportional, Integrated and Differentiated (PID):
where c0 is an offset value. Finally, the scaled output signal is obtained using the output lower bound and upper bound values:
Parameters
Parameter |
input |
unit |
range |
default |
remarks |
---|---|---|---|---|---|
input value to switch ON |
real |
||||
input value to switch OFF |
real |
||||
Reset time (on) |
real |
[s] |
|||
Reset time (off) |
real |
[s] |
|||
Initial status |
ON/ OFF |
||||
Initial setpoint |
real |
Can be overruled by 3rd input channel |
|||
Lower Bound (input) |
real |
||||
Upper Bound (input) |
real |
||||
Accuracy of recorded value |
real |
See remarks |
|||
Sample time interval |
real |
[s] |
See remarks |
||
Type of control |
P/ PI/ PID |
||||
Offset value (bias) |
real |
only if ‘Type of Control” = P |
|||
Gain |
real |
||||
Integration time constant |
real |
[s] |
|||
Initial value of integrator |
real |
only if ‘Type of Control” = PI or PID Can be overruled by 4th input channel |
|||
Start value (output) |
real |
||||
Use stabilize time |
YES/ NO |
||||
Stabilization time |
real |
Only if “Use stabilize time” = YES |
|||
Lower bound (output) |
real |
||||
Upper bound (output) |
real |
||||
Ramp (max. change/sec) |
constant/ variable |
||||
Ramp value |
real |
Only if Ramp = constant |
|||
Ramp value START |
real |
Only if Ramp = variable |
|||
Ramp value STOP |
real |
Only if Ramp = variable |
|||
Ramp value CTRL_UP |
real |
Only if Ramp = variable |
|||
Ramp value CTRL_DOWN |
real |
Only if Ramp = variable |
|||
Output value when OFF |
real |
Remarks
The Sample time interval is used to decrease the resolution of the input signal. A PLC-controller can have a different sample time than the simulation time.
If the difference between the measured (recorded) value and setpoint is smaller than the accuracy, the error is set to zero.
The PID component allows an ‘upper bound’ and a ‘lower bound’ to be imposed on the output signal.
When the output value “hits” the upper or lower bound the control system can not follow the error anymore and has no possibility to feed back to the system. If this situation remains long enough the integrator fills with a large value, which inhibits timely reaction if the error value changes direction (sign). To prevent this, a simple anti-reset windup provision is implemented. This provision suspends the accumulating of the error during the time that the output value violates the lower or upper bound.
Furthermore, a maximum allowable ‘ramp value’ can also be specified to control the rate of change of the output.
The integrating part can be initialised with a non-zero value. This can be used to adjust the PID controller to the hydraulic steady state (see examples).
In the steady state, the error should be equal to zero. This ensures that the entire system is in a true steady state.
It is the user’s responsibility to choose, and so that the output signal can be used by the controlled hydraulic component. For instance, if a valve is the controlled hydraulic component then the PID output signal must have a lower bound of 0 and an upper bound of 1. q
Component Messages
Message |
Explanation |
---|---|
Integrator must be less than upper bound |
Input validation |
Integrator must be greater than lower bound |
Input validation |
Offset must be less than upper bound |
Input validation |
Offset must be greater than lower bound |
Input validation |
Discrepancy between initial state and on/off value |
Switch value must be between (input) lower and upper bounds |
ERROR: Discrepancy with setpoint value more than 25 % |
The control system and hydraulic system must be in equilibrium for the steady state, see remarks |
Discrepancy with setpoint value and measured value |
|
Target below lowerbound, anti-reset windup provision activated |
Informative |
Target above lowerbound, anti-reset windup prov. de-activated |
Informative |
Target above upperbound, anti-reset windup provision activated |
Informative |
Target below upperbound, anti-reset windup prov. de-activated |
Informative |
change to Starting phase |
Informative |
change to Stabalize phase |
Informative |
change to Control phase |
Informative |
change to Off phase |
Informative |
Examples
PID start/stop normalized component controlling discharge with a fluid-level dependent setpoint.