4.21. Pump Energy¶
4.21.1. Pump Energy components¶
A special set H-components are used for the module PumpEnergy. These components are used in combination with the PUMP component. The PumpEnergy components are ignored in the steady and transient calculation.
Overview available components
type |
description |
---|---|
PUMPSCEN |
Pump operation scenario |
Q_PATTRN |
Discharge pattern as function of time |
Q_FREQ |
Discharge frequency in a certain period |
SYSCHAR |
System characteristic |
4.21.1.1. Mathematical model¶
The PumpEnergy module calculates the total power (kW) of a multi-pumpstation (two or more pumps in parallel arrangement) for a specified operation scenario. If the time is specified the total energy (kWh) is calculated as well. For one or more discharge ranges, the user specify which pumps are running. The running pumps can be speed controlled or fixed speed. If they are speed controlled, the program calculates the speed in such way that the required head (as defined by the given system characteristic) is satisfied.
The pump curves of pumps in parallel placement are summarised. Intermediate points are determined by linear interpolation.
For a certain discharge the point of intersection of the summarised pump curve with the specified system characteristic is computed. In case of variable speed pumps, the affinity rules are used:
All variable speed pumps are controlled with the same ratio according:
Subsequently the duty point of each individual pump is determined, that means the discharge and head, but also the efficiency and power and, if the duration is known, the energy.
4.21.2. PUMPSCEN (Pump Scenario)¶

Fig. 4.21.1 Wanda schematic Pump Scenario¶
4.21.2.1. Input specifications¶
description |
input |
unit |
range |
default |
remarks |
---|---|---|---|---|---|
Scenario |
table |
See below |
The scenario table contains all non-disused pumps available in the diagram.
Q from (m3/h) |
Q to (m3/h) |
PUMP 1 (rpm) |
PUMP 2 (rpm) |
PUMP 3 (rpm) |
---|---|---|---|---|
0 |
1200 |
0 |
||
1200 |
2400 |
0 |
||
2400 |
4000 |
1500 |
0 |
For each discharge range (phase) the operating pumps are defined:
value = 0 (zero) means a variable speed pump
value > 0 means the actual fixed speed
empty field means pump is not operating
4.21.2.2. Output specifications¶
If the pump energy can be computed (depends of Q_PATTRN or Q_FREQ component), the energy consumption for each phase is mentioned in the scenario table. A separate output property is used for the total energy amount.
Q from |
Q to |
PUMP 1 |
PUMP 2 |
PUMP 3 |
Energy |
Energy ratio |
---|---|---|---|---|---|---|
(m3/h) |
(m3/h) |
(rpm) |
(rpm) |
(rpm) |
(MWh) |
(%) |
The output properties are:
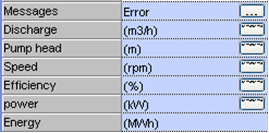
Fig. 4.21.2 Display of the output properties¶
The message property contains messages with respect to all components use for the PumpEnergy calculation;
Next output properties can be visualised in a chart as function of discharge or time (last one only in combination with Q_PATTRN)
Discharge
Head
Speed
Efficiency
Power
In the example the coherence of the Pump Energy components are explained.
4.21.3. Q_PATTRN (discharge pattern)¶

Fig. 4.21.3 Wanda schematic Pump discharge pattern¶
4.21.3.1. Input properties¶
description |
input |
unit |
range |
default |
remarks |
---|---|---|---|---|---|
Discharge pattern |
table |
See below |
The discharge pattern table is a 2-columns table
Time (s) |
Discharge (m3/s) |
---|---|
Real |
Real |
Example:
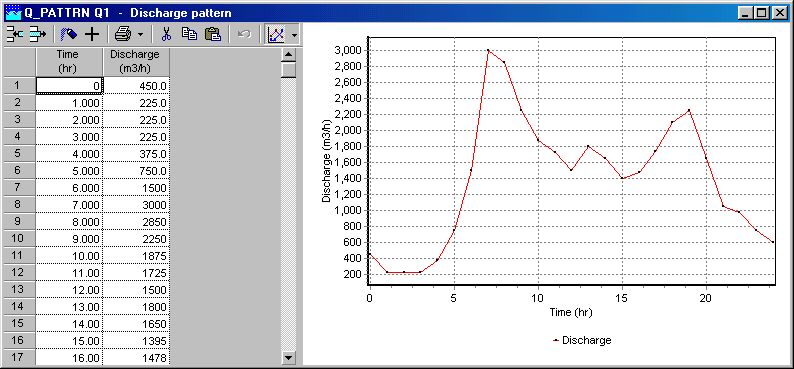
Fig. 4.21.4 Example of discharge pattern¶
4.21.3.2. Output properties¶
None
4.21.4. Q_FREQ (discharge frequency)¶

Fig. 4.21.5 Wanda schematic Pump discharge frequency¶
4.21.4.1. Input properties¶
description |
input |
unit |
range |
default |
remarks |
---|---|---|---|---|---|
Discharge frequency |
table |
See below |
The discharge pattern table is a 3-columns table; column one and two are used to specify the range, only the second column can be edit; the first column is automatically filled, starting with zero.
Q from (m3/s) |
Q to (m3/s) |
Time (s) |
---|---|---|
Real |
Real |
Real |
Example:
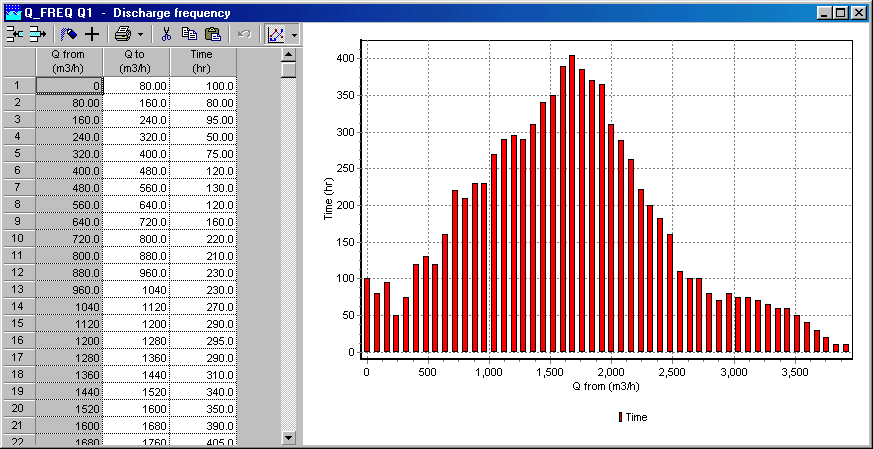
Fig. 4.21.6 Discharge frequency example¶
4.21.4.2. Output properties¶
None
4.21.5. SYSCHAR (System characteristic)¶

Fig. 4.21.7 Wanda schematic system characteristic¶
4.21.5.1. Input properties¶
description |
input |
unit |
range |
default |
remarks |
---|---|---|---|---|---|
System characteristic |
table |
See below |
The system characteristic is a 2-columns table;
Discharge (m3/s) |
Pump head (m) |
---|---|
Real |
Real |
Example:
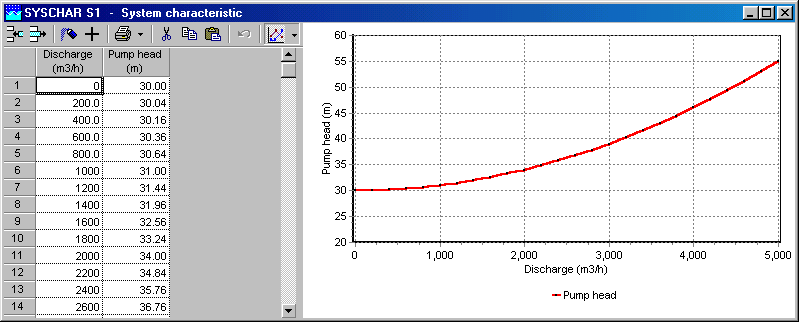
Fig. 4.21.8 Example of the system characteristic table.¶
The Pump Head is defined as the sum of the static head and dynamic head:
Note: this characteristic can be derived form the System Characteristic module.
See also “System characteristic” (Section 2.14.7)
Create the wanted system characteristic, show the chart and copy the chart data to the clipboard.
Next, copy the chart data into the SYSCHAR table.
4.21.5.2. Output properties¶
None
4.21.5.3. Example¶
A pumpstation with three different pumps supplies to a drinking water network. The maximum delivery rate is 4000 m3/h. From history reports the annual delivery ranges are known (see chart given by Q_FREQ)
Note: this example is included in the example directory
The desired pressure in the network (pressure side pump) is defined by the system characteristic:
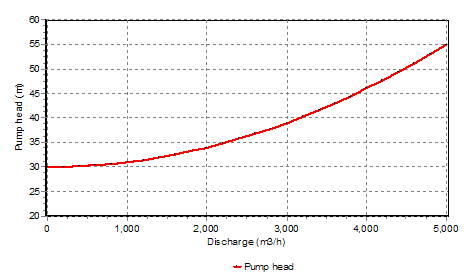
Fig. 4.21.9 Pump discharge versus pump head.¶
Pumpdata:
Pump id |
design capacity (m3/h) |
Rated speed curve (rpm) |
min speed (rpm) |
max speed (rpm) |
max power (kW) |
---|---|---|---|---|---|
1000 |
1000 |
1200 |
1000 |
1500 |
150 |
1300 |
1300 |
1200 |
1000 |
1500 |
200 |
1800 |
1800 |
1200 |
1000 |
1500 |
300 |
The pump curves are given below:
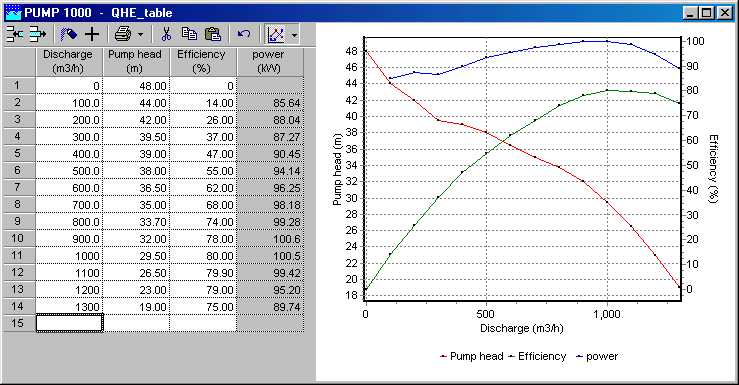
Fig. 4.21.10 Pump curve for pump 10000¶
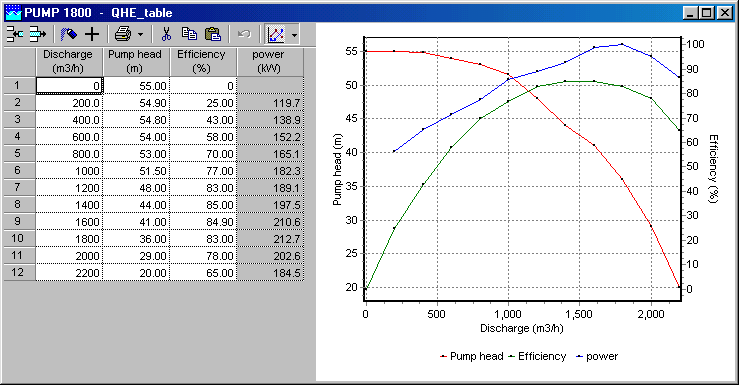
Fig. 4.21.11 Pump curve for pump 1800¶
Question: Optimise the pump scenario.
Step 1: add components into diagram:
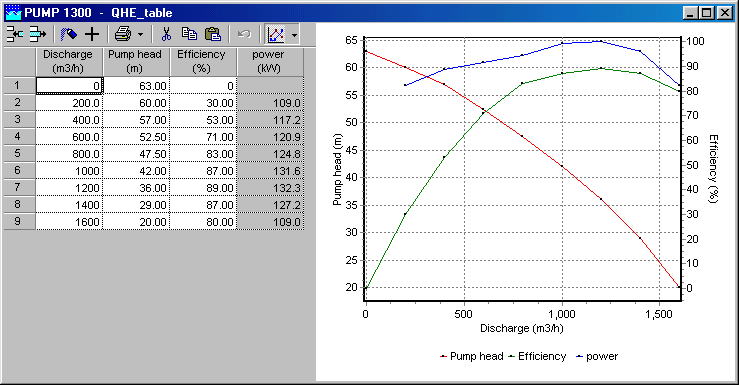
Fig. 4.21.12 Additional pump curve for pump 1300¶
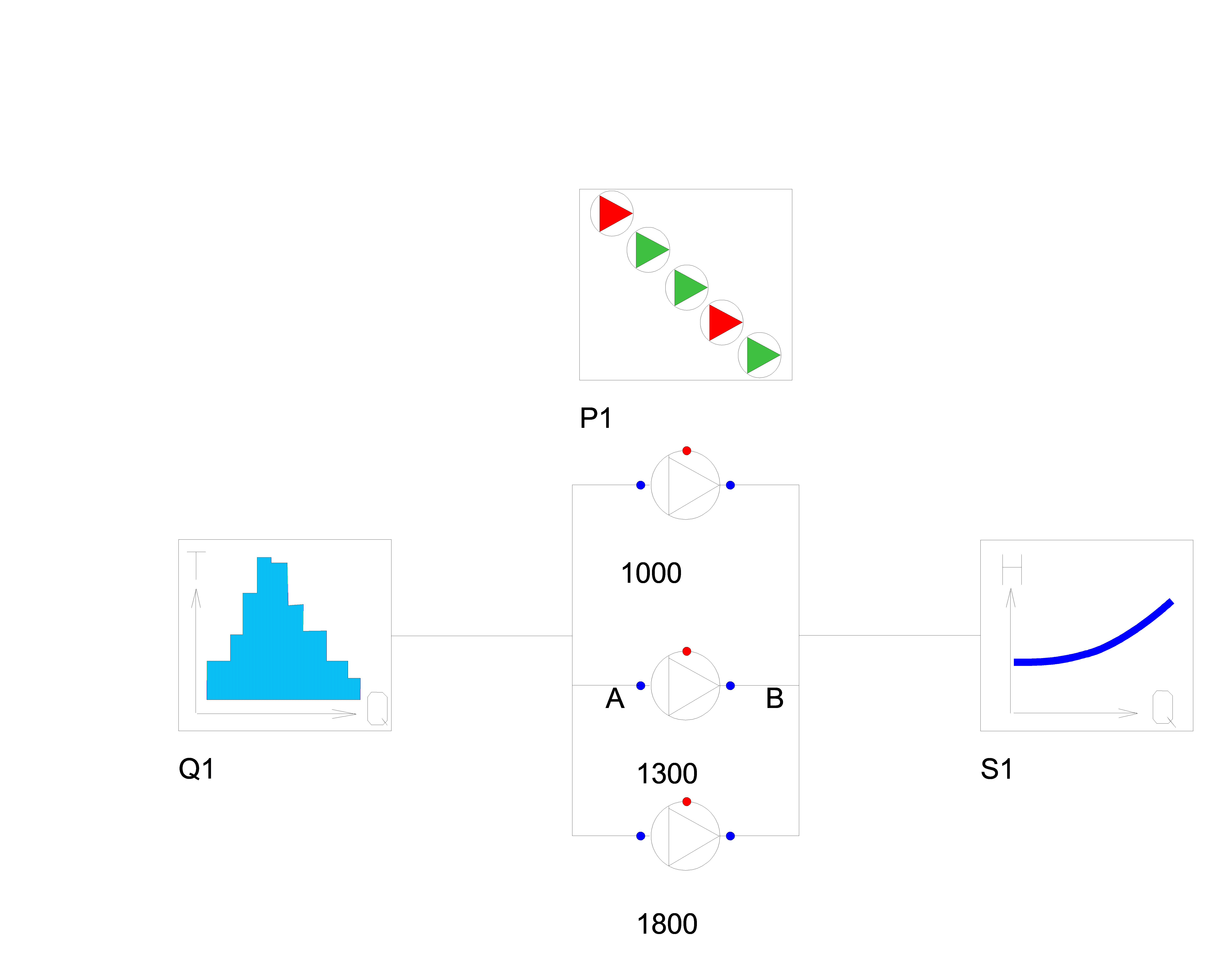
Fig. 4.21.13 Schematic overview of Wanda model.¶
Step 2: input of pump data and system characteristic
Step 3: choose a scenario
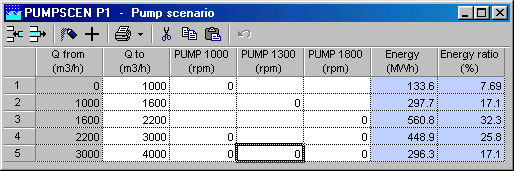
Fig. 4.21.14 Scenario management table¶
The total energy consumption (annual base according specified frequency) is 1737 MWh
Step 4: analyse the scenario output (especially efficient)
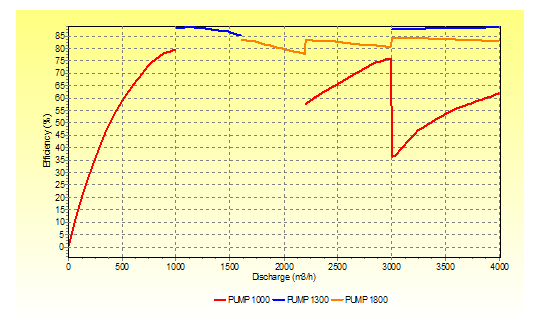
Fig. 4.21.15 Scenario output (graph)¶
Step 5: adapt the scenario
Pump 1300 has a better efficiency, use this pump also in the first stage and fourth stage n stead of Pump 1000. The last stage, use Pump 1000 at a fixed speed of 1350 rpm.
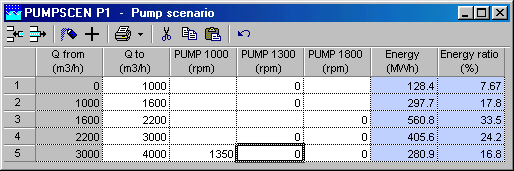
Fig. 4.21.16 Optimized pump scenario.¶
The total energy consumption is now reduced to 1673 MWh; that means a reduction of 4 %.
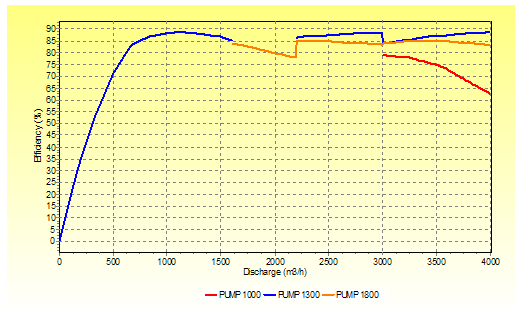
Fig. 4.21.17 Optimized pump scenario result.¶
Step 6: analyse a 24 hours period
Replace the Q_FREQ by the Q_PATTRN and specify the discharge pattern
Note: it is not necessary to connect the Q_PATTRN to the pumps
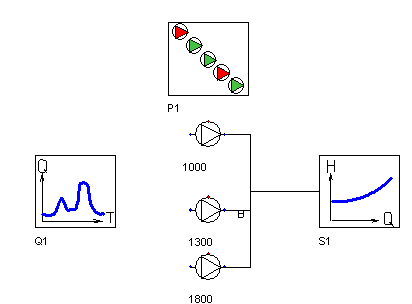
Fig. 4.21.18 Altered Wanda schematic.¶
Step 7: Specify data for Q_PATTRN
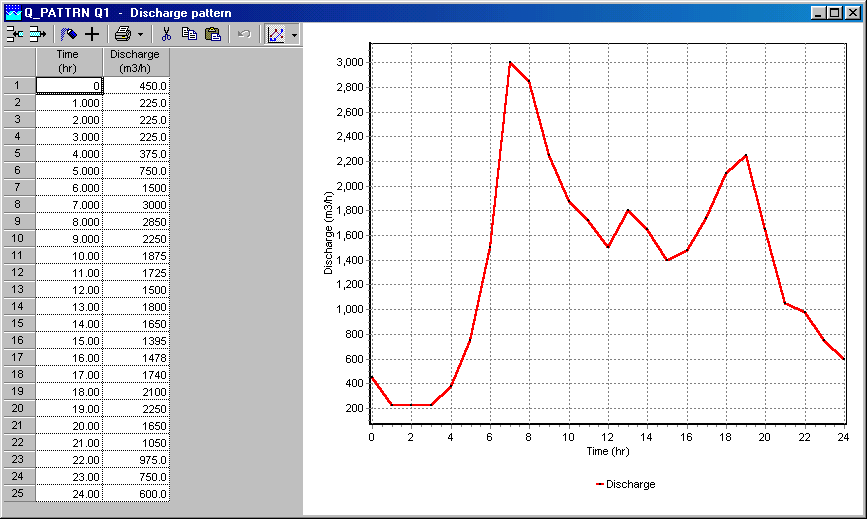
Fig. 4.21.19 Discharge pattern for the pumps.¶
Step 8: analyse the results
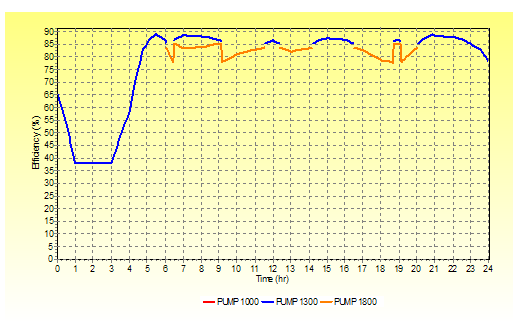
Fig. 4.21.20 Results of the changed discharge pattern for time versus efficiency.¶
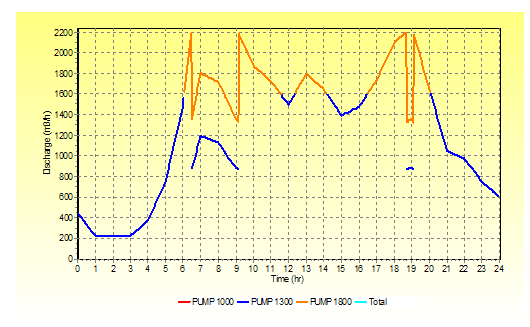
Fig. 4.21.21 Results of the changed discharge pattern for time versus discharge.¶
Advise: use for the low discharges (0 – 400 m3/h) a pump with lower capacity.